All You Need to Know About Diaphragm valve – Diaphragm Valve Functionthermostatic balancing valve
Diaphragm valves consists of a valve body with two or more ports, a diaphragm, and a “weir or saddle” or seat upon which the diaphragm closes the valve. The diaphragm valve was initially developed for industrial applications and pipe-organs. Later on the design was adapted for use in the bio-pharmaceutical industry by using compliant materials that can withstand sanitizing and sterilizing methods. What’s more, sanitary diaphragm valves are specially designed with the highest standard for applications in manufacturing of medicine and food.
What is a Diaphragm Valve?
Diaphragm valves are bi-directional, on-off throttle valves. They are used to control fluid flow by regulating the area with which media can enter and exit the valve, effectively changing its speed and velocity. They are so-called “diaphragm” valves because a thin, flexible membrane is used to control the opening and closing of the valve. They can be made with metal such as stainless steel, plastic, and even single-use materials. Diaphragm valves are like pinch valves but they use a linear compressor which pushes the thin diaphragm into contact with the valve body. They offer discrete and variable pressure control and can be both manually and automatically actuated. Diaphragm valves are clean, leak-proof, easy to maintain, safe, and effective valves that are best suited for moderate pressure & temperature applications which require stop/start fluid control.
How do a Diaphragm Valve operate?
Their operation is not unlike controlling the flow of water through a flexible hose by pinching the hose. These valves are well suited for flows containing solid particulate matter such as slurries, although precise throttling may be difficult to achieve due to the elasticity of the diaphragm.
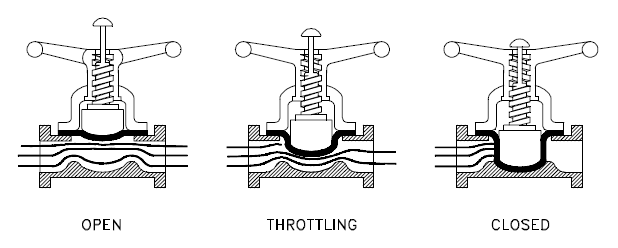
Types of Diaphragm Valves
Wire type diaphragm valve
The most common available designs are the weir-type diaphragm valve. The elevated lip/saddle configuration for limited flow control is ideally suitable and is safely leaked thanks to the cover over the diaphragm and actuator. This design is suitable for harmful or corrosive gas and liquids, as this cover keeps every breakdown of the membrane. As an integrated element of the valve body, a weir is given. The weir serves as the valve seat to compress the diaphragm to avoid the surge. The inclined body often naturally drains this valve, although it may occur in both directions and with certain uses, that might not be desirable. Generally, this type of diaphragm valve is manufactured in large sizes. The elevated weir decreases the amount of movement of the diaphragm from the completely open position to the completely closed position, thus decreasing the amount of strain and stress in the diaphragm. For smooth, homogenous fluids, the weir-type valve is often used, as viscous slurries and sediments can build up on either side of the saddle. In processes such as food/chemical, gas processing, corrosive, and water applications, they are most commonly found.
Straight through diaphragm valve
The straight-through diaphragm valve is similar in appearance to the weir-types; but, it does not include the typical saddle and instead has a straight track. Usually, their membranes are more compact and allow for a longer distance to pass, since the very bottom of the valve must be touched. When the straight-through valve is open, for maximum streamline flow in any direction, the diaphragm lifts high. When the valve is closed, even with coarse or fibrous material in the line, the diaphragm seals tight for positive sealing. These valves must also be repaired because owing to their more compact membranes, their lifetime is normally shorter than weir-type designs. For slurries, viscous oils, and other conditions, where blocking must be minimized, straight through diaphragm valves are often used. In the beverage industry, the full-bore type of valve is most commonly used. It enables ball-brush cleaning, without opening or removing the valve from the line, with either steam or caustic soda. They are also suitable for bi-directional flow regimes since there is no saddle to avoid the sudden transition from inlet to outlet.
Diaphragm Valve Function
The diaphragm is connected to a compressor by a stud molded into the diaphragm. To start or increase flow the compressor is moved up by the valve stem. To stop or slow flow, the compressor is lowered and the diaphragm is pressed against the bottom of the valve. Diaphragm valves are excellent for controlling the flow of fluids containing suspended solids and offer the flexibility of being installed in any position. Weir-type diaphragm valves are better at throttling than straight though diaphragm valves because the design’s large shutoff area along the seat gives it the characteristics of a quick-opening valve. The diaphragm acts as the gasket of the valve to seal against leaks between the body and bonnet cap.
Diaphragm valves use a corrosion-resistant lining valve body and a corrosion-resistant diaphragm to replace the valve plug components, and control the medium by moving the diaphragm. When the diaphragm is lifted up, the passage is opened; when the diaphragm is lowered, it is pressed against the valve body and the valve is closed.

Advantages of Diaphragm valve
- 1) Simple structure, consisting of only three parts: a valve body, a diaphragm and a cover
- 2) During the operation, the medium only contacts with the diaphragm, so the valve is not easily contaminated.
- 3) Suitable for transporting corrosive, viscous liquids
Disadvantages of Diaphragm valve
- 1) Not suitable for larger pipe diameters
- 2) Poor pressure resistance and temperature resistance
Diaphragm Material Of Construction
Diaphragms can be made from a variety of materials. The material choice is based on the nature of the material handled, temperature, pressure, and frequency of operation. Elastomeric diaphragm materials are highly resistant to chemicals at high temperatures. However, the mechanical properties of elastomeric materials will be weakened at a higher temperature (above 150°F). High pressure can also destroy the diaphragm. Another factor that can affect the diaphragm function is the concentration of the media it will handle. The material may exhibit satisfactory corrosion resistance to certain corrodents up to a specific concentration and/or temperature. Examples of diaphragm material and their specifications can be seen in the chart below.
Material | Size | Temperature | Applications | ||
inches | mm | ºF | ºC | ||
Butyl rubber | 0.6 – 14 | 15 – 350 | – 22 to 134 | – 30 to 90 | Acids and alkalis |
Nitril rubber | 0.6 – 14 | 15 – 350 | 14 to 134 | -10 to 90 | Oils, fats and fuels |
Neoprene | 0.6 – 14 | 15 – 350 | – 4 to 134 | – 20 to 90 | Oils, greases, air and radioactive fluids |
Natural/synthetic rubber | 0.6 – 14 | 15 – 350 | – 40 to 134 | – 40 to 90 | Abrasives, brewing and dilute mineral acids |
White natural rubber | 0.6 – 5 | 15 – 125 | – 31 to 134 | – 35 to 90 | Foods and pharmaceuticals |
White butyl | 0.6 – 6 | 15 – 150 | – 22 to 212 | – 30 to 100 | Natural color, food, plastics and pharmaceuticals |
Viton | 0.6 – 14 | 15 – 350 | 41 to 284 | 5 to 140 | Hydrocarbon acids, sulphture and chlorine applications |
Hypalon | 0.6 – 14 | 15 – 350 | 32 to 134 | 0 to 90 | Acid and ozone resistant |
Butyl rubber | 0.6 – 14 | 15 – 350 | – 4 to 248 | – 20 to 120 | Hot water and intermittent steam services, sugar refining |
Related Tags :
Ten articles before and after
Sanitary Valves for Industrial Perfume Manufacturing
How to Maintain the Sanitary Diaphragm Valves? – Zeco Valve
Press Drop: An Important Selection Criteria for Choosing Control Valves – Zeco Valve
Maintenance of Sanitary Pneumatic Ball Valve – Zeco Valve
How Does Sanitary Ball Valve Work? – Zeco Valve
Sanitary Ball Valve Image Gallery – Zeco Valve
Categories of pressure relief valves and their applications – Zeco Valve
Differences Between Sanitary Valves And Industrial Valves
Sanitary Diaphragm Valve Image Gallery – Zeco Valve
4 Metrics for the Quality of Sanitary Pneumatic Ball Valves – Zeco Valve