Forged Steel Gate Valve
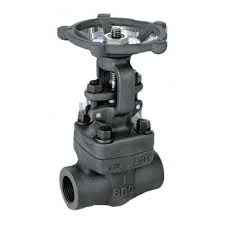
The Application of Forged Steel Gate Valve
The Forged Steel Gate Valve is a robust and versatile component used in various industrial applications, including as a cooling tower isolation valve. Engineered by leading manufacturers like Rotork and Cameron, these valves are designed to withstand high-pressure and high-temperature environments commonly found in industrial settings. Their durable construction, often made of forged steel, ensures reliability and longevity, making them ideal for critical isolation applications in cooling tower systems. Cooling tower valves companies rely on these gate valves for their superior sealing capabilities and minimal leakage, ensuring efficient and safe operation of cooling tower systems. Whether in power plants, refineries, or chemical processing plants, the Forged Steel Gate Valve provides dependable performance, contributing to the smooth functioning of industrial processes.
What Is Forged Steel Gate Valve?
A Forged Steel Gate Valve is a type of industrial valve specifically designed for high-pressure and high-temperature applications. It features a sturdy construction, typically made from forged steel, which enhances its strength and durability. The gate valve mechanism consists of a gate (or wedge) that moves up and down to control the flow of fluids through the valve. When the valve is open, the gate is lifted to allow fluid passage, and when closed, the gate is lowered to block the flow completely. This design makes Forged Steel Gate Valves suitable for various industries, including oil and gas, petrochemical, power generation, and refining, where reliable isolation and control of fluids are critical.
Features of Forged Steel Gate Valve
- OS&Y, Rising Stem: This feature ensures that the valve’s position is clearly visible, allowing operators to monitor whether it’s open or closed. The stem rises as the valve opens, providing a visual indication of its status.
- Solid Wedge: The valve’s gate or wedge is solid, offering robust and reliable shut-off capabilities. This design minimizes the risk of leakage by providing a tight seal against the valve seat.
- Graphite Packing and Gasket: Graphite packing and gaskets are used to create a secure seal around the valve stem, preventing leakage of the fluid being controlled by the valve. Graphite’s durability and resistance to high temperatures make it an ideal choice for this purpose.
- Two Piece Self-aligning Packing Gland: This feature ensures proper alignment of the packing gland, which helps maintain the integrity of the seal around the valve stem. The two-piece design simplifies maintenance and replacement of packing components.
- Bolted Bonnet with Spiral-wound Gasket: The bolted bonnet secures the valve’s components in place, while the spiral-wound gasket provides a reliable seal between the bonnet and the body of the valve. This construction enhances the valve’s resistance to pressure and temperature extremes.
- Integral Backseat: The integral backseat feature allows the valve to be safely operated even when fully open, providing a secondary seal to prevent leakage through the stem packing.
- Optional Feature: This indicates that additional features or configurations may be available to suit specific application requirements or preferences, providing flexibility in valve design and functionality.
Advantages of Forged Steel Gate Valve
- High Strength: Forged steel gate valves are manufactured using a forging process, resulting in a sturdy and durable construction that can withstand high pressure and temperature conditions.
- Excellent Sealing: The solid wedge design of forged steel gate valves provides a tight seal against the valve seat, minimizing leakage and ensuring reliable shut-off capabilities.
- Versatility: These valves are suitable for various applications across industries such as oil and gas, petrochemical, power generation, and more, making them highly versatile.
- Resistant to Corrosion: The materials used in forged steel gate valves are resistant to corrosion, ensuring longevity and reliability even in harsh operating environments.
- Low Maintenance: With fewer moving parts and robust construction, forged steel gate valves require minimal maintenance, reducing downtime and operating costs.
- Wide Range of Sizes and Pressure Ratings: These valves are available in a wide range of sizes and pressure ratings, allowing for flexibility in design and application.
- Long Service Life: Due to their robust construction and high-quality materials, forged steel gate valves offer a long service life, providing dependable performance over time.
The Specifications of Forged Steel Gate Valve
Specification | Details |
---|---|
Type | Forged Steel Gate Valve |
Ball Material | N/A |
Attachment Type | Flanged, Threaded, Welded |
Thread Standard | ANSI, API, DIN, BS |
Thread Size | Various sizes depending on the valve size |
Body Material | Forged Steel |
Safe for Use With | Various fluids, gases, and steam |
Handle Type | Handwheel, Gear, Actuator |
Handle Material | Carbon Steel, Stainless Steel, Aluminum |
Maximum Working Pressure (psi) | Up to 2500 psi (higher pressures available on request) |
Maximum Working Pressure (bar) | Up to 172 bar (higher pressures available on request) |
Operating Pressure | Typically follows the working pressure range |
The Parameter of Forged Steel Gate Valve
- Type: Forged Steel Gate Valve
- Body Material: Made of forged steel for enhanced strength and durability.
- Attachment Options: Available with various attachment types including flanged, threaded, and welded connections.
- Thread Standards: Compliant with ANSI, API, DIN, BS standards for seamless integration into different systems.
- Thread Sizes: Available in various sizes to suit different applications and piping requirements.
- Handle Types: Equipped with different handle options such as handwheel, gear, or actuator for manual or automated operation.
- Maximum Working Pressure (psi): Can handle pressures up to 2500 psi, with higher pressures available upon request.
- Maximum Working Pressure (bar): Capable of withstanding pressures up to 172 bar, with higher ratings available as needed.
- Safe for Use With: Suitable for use with various fluids, gases, and steam applications.
- Operating Pressure: Typically operates within the specified working pressure range to ensure optimal performance and reliability.
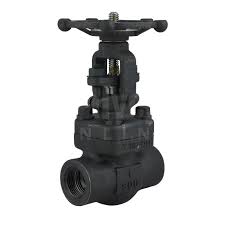
The Parameter of Forged Steel Gate Valve
The operation theory of a Forged Steel Gate Valve involves a rising stem design, where the stem moves up and down to control the position of the gate. When the valve is open, the gate rises to allow fluid flow, and when closed, the gate descends to block the flow. This design ensures a tight seal when fully closed, minimizing leakage.
In contrast to ball valves, which use a rotating ball to control flow, and globe valves, which utilize a plug-like disc, gate valves rely on the movement of a gate (typically wedge-shaped) to regulate flow. The gate moves perpendicular to the flow direction, providing a straight-through path for fluid when fully open and a complete blockage when fully closed.
Gate valves are often preferred in applications where a straight-through flow path is desired, and they excel in applications requiring tight shut-off and minimal flow restriction. Their operation is straightforward, offering reliable control over fluid flow in various industrial processes.
The Parameters Table of Forged Steel Gate Valve
Parameter | Specification |
---|---|
Type | Industrial Gate Valve |
Body Material | Cast Iron, Ductile Iron, Carbon Steel, Stainless Steel |
Bonnet Material | Cast Iron, Ductile Iron, Carbon Steel, Stainless Steel |
Disc Material | Cast Iron, Ductile Iron, Carbon Steel, Stainless Steel |
Stem Material | Stainless Steel, Carbon Steel |
Seat Material | Brass, Stainless Steel, Bronze, EPDM, PTFE |
Seal Material | Nitrile, EPDM, Viton, PTFE |
End Connection | Flanged, Threaded, Socket Weld, Butt Weld |
Size Range | 2″ – 48″ (50mm – 1200mm) |
Pressure Rating | Class 150 – Class 2500 |
Operating Temperature | -20°C to 400°C (-4°F to 752°F) |
Suitable Media | Water, Oil, Gas, Steam, Chemicals |
Actuation | Manual, Electric, Pneumatic, Hydraulic |