8 inch Butterfly Valve
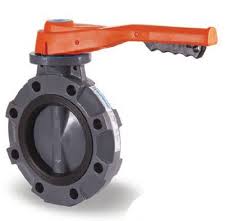
The Application of 8″ Butterfly Valve
The 8″ Butterfly Valve is a cornerstone of fluid control systems, offering versatility and efficiency. Engineered to DSI gate valve standards, it ensures optimal performance across industries, alongside DSI valves USA counterparts like DSI check valve and DSI globe valve for seamless flow regulation.
Built with resilience akin to DSI 37XUF gate valve, it’s fortified by DSI cast steel gate valves. The addition of a butterfly check valve mechanism enhances functionality.
Innovation from Cameron shines through features like butterfly valve seat technology, ensuring longevity with materials like A350 LF2. Available in various sizes, including 8″, it meets specific demands.
Adhering to Cameron brass ball valve standards, this butterfly valve assures top-tier performance, ensuring seamless operations in oil and gas, water treatment, and beyond.
Advantages of 1 in Ball Valves
- Inline quarter-turn valve shuts air flow to air line on or off
- Solid brass body for long-life corrosion resistance
- Can also be used as moisture drain on system
- Adjustable stem packing nut
The Parameter of 8″ Butterfly Valve
- Valve Size: 8 inches, suitable for medium-sized pipelines.
- Pressure Rating: Typically ANSI 150 or ANSI 300, ensuring compatibility with various pressure levels.
- Temperature Range: Standard operating temperature ranges from -20°C to 200°C (-4°F to 392°F), suitable for most industrial applications.
- Body Material: Constructed from durable materials such as stainless steel, carbon steel, or ductile iron.
- Disc Material: Made of corrosion-resistant materials like stainless steel or ductile iron for longevity.
- Seat Material: Utilizes resilient materials such as EPDM or PTFE for reliable sealing.
- Actuation Type: Compatible with manual, pneumatic, or electric actuators for flexible operation.
- End Connection: Available with flanged, wafer, or lug end connections for easy installation.
- Leakage Rate: Engineered to meet industry standards for minimal leakage, ensuring efficient operation.
- Fire Safety: May feature fireproof seat design and metal-to-metal seals to withstand high temperatures.
- Compliance: Complies with industry standards such as API, ANSI, and ISO for quality assurance.
- Maintenance: Designed for easy maintenance with features like replaceable seats and seals, reducing downtime.
- Accessories: Compatible with various accessories like positioners, limit switches, and actuators for enhanced functionality.
The Operation Theory of 8″ Butterfly Valve
The operation theory of an 8″ Butterfly Valve involves the rotation of a disc perpendicular to fluid flow for control. This design, akin to INTEC Duoball Valve, ensures efficient regulation compliant with API 608 standards. Manufactured by leading industrial valve manufacturers like DSI, known for forged steel valves, it’s often featured in their gate valve catalogue.
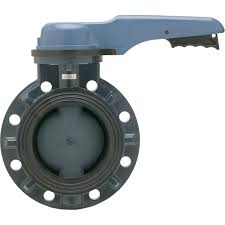
The Parameters Table of 8″ Butterfly Valve
Parameter | Description |
---|---|
Valve Size | 8 inches |
Pressure Rating | ANSI 150, ANSI 300, etc. |
Temperature Range | -20°C to 200°C (-4°F to 392°F) |
Body Material | Stainless steel, carbon steel, ductile iron |
Disc Material | Stainless steel, ductile iron, aluminum |
Seat Material | EPDM, PTFE, metal-to-metal |
Actuation Type | Manual, pneumatic, electric |
End Connection | Flanged, wafer, lug |
Leakage Rate | Meets or exceeds industry standards |
Fire Safety | Fireproof seat design, metal-to-metal seals |
Compliance | API 608, ANSI, ISO |
Maintenance | Replaceable seats and seals for easy upkeep |
Accessories | Compatible with various actuators, limit switches |
Relevant Information about 8″ Butterfly Valve
- Rotor: The rotor is the rotating part of the valve responsible for controlling the flow of fluid. In a butterfly valve, it’s the disc that pivots to open or close the flow path.
- Stator: The stator refers to the stationary part of the valve, typically the valve body and seat. It provides support and creates a sealing surface for the rotor to operate against.
- Universal Joint: The universal joint connects the actuator to the valve shaft, allowing for rotational movement. It ensures that the motion from the actuator is accurately transmitted to the valve.
- Shaft Seal: The shaft seal prevents leakage along the valve shaft where it passes through the valve body. It’s a crucial component for maintaining the integrity of the valve and preventing fluid loss.
- Driving System: The driving system consists of the actuator and associated mechanisms that provide the force to operate the valve. It can be manual, pneumatic, or electric, depending on the application requirements.