Emergency Shutdown Valves for Industrial Safety
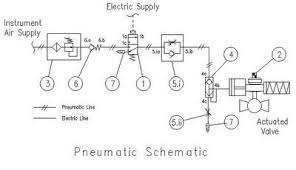
The Application of Emergency Shutdown Valves
In the realm of emergency shutdown valves, Cameron stands out as a leading manufacturer renowned for its expertise and innovation. These valves play a critical role in various industrial applications, ensuring safety and protection against unforeseen circumstances. The emergency shutdown valve operation involves swift and automatic closure upon detection of abnormal conditions, such as excessive pressure or leakage, preventing potential hazards. Their working principle relies on sensors or triggers to initiate immediate valve closure, halting the flow of fluids and averting accidents. Industries ranging from oil and gas production to chemical processing rely on emergency shutdown valves to safeguard personnel, equipment, and the environment. With Cameron’s commitment to excellence, these valves continue to set the standard for reliability and performance in critical safety systems.
What Are The Types Of Emergency Shutdown Valves?
- Gate Valve: Gate valves are widely used as emergency shutdown valves due to their ability to provide a tight seal and quick closure. They operate by raising or lowering a gate to control the flow of fluid, and in emergency situations, they can be closed rapidly to stop the flow entirely.
- Ball Valve: Ball valves are another popular choice for emergency shutdown applications. Their simple design allows for quick operation, and they offer excellent sealing properties, ensuring reliable shut-off during emergencies.
- Butterfly Valve: Butterfly valves are suitable for large-diameter pipelines and high-flow applications. In emergency situations, they can be closed by rotating a disc perpendicular to the flow direction, effectively blocking the flow of fluid.
- Diaphragm Valve: Diaphragm valves feature a flexible diaphragm that acts as a barrier to regulate fluid flow. During emergencies, the diaphragm can be quickly closed to prevent further flow, making them suitable for controlling hazardous fluids.
- Pilot-Operated Valve: Pilot-operated valves use a smaller valve (pilot valve) to control the operation of a larger valve. They are often used in critical systems where precise control and fail-safe operation are required.
- Check Valve: Check valves allow fluid to flow in one direction only. In emergency situations, they can prevent backflow and maintain system integrity by automatically closing to block reverse flow.
What Is Emergency Shutdown Valves?
Emergency shutdown valves are critical safety devices installed in industrial systems to swiftly halt the flow of fluids in emergency situations. These valves are designed to automatically close upon detection of abnormal conditions such as excessive pressure, leakage, or other hazards. Their primary function is to protect personnel, equipment, and the environment by preventing the escalation of emergencies. Emergency shutdown valves play a crucial role in various industries, including oil and gas, chemical processing, power generation, and more, where rapid response to hazardous situations is paramount for ensuring safety and minimizing risks.
How Does Emergency Shutdown Valves work?
Emergency shutdown valves operate through automated systems that detect abnormal conditions such as high pressure, leakage, or fire. When triggered, these systems send signals to the valves to initiate immediate closure. The valves swiftly shut off the flow of fluids, preventing further escalation of the emergency. This rapid response is essential for safeguarding personnel, equipment, and the environment in critical industrial processes.
Features of Emergency Shutdown Valves
- Rapid Response: Emergency shutdown valves offer swift closure in critical situations, minimizing the potential for accidents and hazards.
- Automatic Operation: They are designed to operate automatically upon detection of abnormal conditions, reducing the reliance on manual intervention and ensuring timely response.
- Reliable Sealing: The valves feature robust sealing mechanisms to provide a tight closure, preventing leakage and maintaining system integrity.
- Versatility: They can be customized to suit various applications and industries, from oil and gas to chemical processing and power generation.
- Safety Compliance: Emergency shutdown valves adhere to stringent safety standards and regulations, ensuring compliance and enhancing overall system safety.
- Remote Control: Some models are equipped with remote control capabilities, allowing operators to initiate closure from a safe distance in emergency situations.
- Fail-Safe Design: They incorporate fail-safe features to ensure operation even in the event of power loss or system failure, enhancing reliability and performance.
- Monitoring Capabilities: Advanced models may include monitoring systems to provide real-time feedback on valve status and performance, facilitating proactive maintenance and troubleshooting.
Advantages of Emergency Shutdown Valves
- Enhanced Safety: Emergency shutdown valves significantly improve safety by swiftly halting the flow of fluids in critical situations, minimizing the risk of accidents and potential hazards.
- Protection of Personnel and Equipment: By quickly shutting off the flow, these valves safeguard personnel, equipment, and the environment from the consequences of emergencies such as leaks, fires, or overpressure.
- Prevent Escalation: Their rapid response helps prevent the escalation of emergencies, mitigating potential damage to the system and surrounding infrastructure.
- Compliance with Regulations: Emergency shutdown valves ensure compliance with safety regulations and standards, enhancing overall system reliability and integrity.
- Minimize Downtime: By promptly addressing emergencies, these valves help minimize downtime and production losses, ensuring continuous operation and business continuity.
- Versatility: They can be applied in various industries and applications, providing flexible solutions for different operational needs and scenarios.
- Remote Operation: Some models offer remote operation capabilities, allowing for quick response and control from a safe location, enhancing operator safety and efficiency.
- Proactive Maintenance: Advanced models may include monitoring systems that provide real-time feedback on valve status, facilitating proactive maintenance and troubleshooting, thus improving overall system reliability.
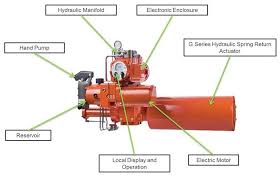
The Specifications of Emergency Shutdown Valves
Specification | Details |
---|---|
Type | Ball Valve |
Ball Material | Stainless Steel |
Attachment Type | Flanged |
Thread Standard | N/A |
Thread Size | N/A |
Body Material | Carbon Steel |
Safe for Use With | Gas, Oil, Water |
Handle Type | Lever |
Handle Material | Stainless Steel |
Maximum Working Pressure psi | 1500 psi |
Maximum Working Pressure bar | 103.42 bar |
Operating Pressure | 0-1200 psi |
The Installation Steps for Emergency Shutdown Valves
- Preparation:
- Gather necessary tools and equipment, including wrenches, bolts, and gaskets.
- Ensure the valve and pipeline are clean and free from debris.
- Positioning:
- Determine the optimal location for the emergency shutdown valve in the pipeline.
- Ensure sufficient space for valve operation and maintenance access.
- Shut Off Supply:
- Turn off the main supply valve to stop the flow of fluid in the pipeline.
- Release any remaining pressure in the system by opening relief valves.
- Measure and Mark:
- Measure and mark the pipeline at the installation point according to the valve size.
- Use a level to ensure accurate alignment.
- Cut Pipe:
- Cut the pipeline at the marked location using a pipe cutter or saw.
- Ensure the cut is clean and free from burrs or irregularities.
- Prepare Valve and Pipeline:
- Apply pipe sealant or Teflon tape to the threaded ends of the valve and pipeline.
- Install gaskets and bolts as necessary for flanged connections.
- Attach Valve to Pipeline:
- Position the valve in place and align it with the cut ends of the pipeline.
- Securely fasten the valve to the pipeline using bolts or other appropriate fasteners.
- Tighten Connections:
- Use wrenches to tighten the connections between the valve and pipeline.
- Ensure all connections are snug and leak-free.
- Test for Leaks:
- Slowly open the main supply valve to allow fluid into the system.
- Check all connections and joints for leaks using a soapy water solution or leak detector.
- Finalize Installation:
- Once all connections are confirmed to be leak-free, operate the valve to ensure proper functionality.
- Securely anchor the valve to nearby structures or supports if necessary.
- Label the valve for easy identification and future maintenance.
The Operation Theory of Emergency Shutdown Valves
- Operation Theory:
- ESVs are designed to automatically close in response to specific hazardous conditions such as excessive pressure, leakage, or fire.
- They are typically equipped with sensors or detectors that continuously monitor critical parameters in the system.
- When abnormal conditions are detected, the ESV actuator is triggered, initiating the valve closure process.
- Emergency Shutdown Valve Actuator:
- The actuator is the component responsible for initiating the closure of the ESV.
- Actuators can be pneumatic, hydraulic, electric, or manual, depending on the application and system requirements.
- Pneumatic actuators are commonly used for their quick response and reliability in emergency situations.
- Emergency Shutdown Valve Closing Time:
- ESV closing time refers to the duration it takes for the valve to fully close once the actuator is activated.
- The closing time is a critical parameter in determining the effectiveness of the ESV in mitigating hazards.
- Faster closing times are generally preferred to minimize the impact of emergencies and prevent further escalation of risks.
The Parameters Table of Emergency Shutdown Valves
Parameter | Material |
---|---|
Valve Body | Stainless Steel, Carbon Steel, Brass, Cast Iron, PVC, etc. |
Valve Seat | PTFE (Teflon), Viton, EPDM, Nitrile, Metal-to-metal, etc. |
Valve Ball | Stainless Steel, Brass, Chrome-plated Brass, Bronze, etc. |
Actuator | Pneumatic: Aluminum, Stainless Steel, Carbon Steel, etc. <br> Hydraulic: Aluminum, Stainless Steel, Carbon Steel, etc. <br> Electric: Stainless Steel, Aluminum, Plastic, etc. |
Valve Stem | Stainless Steel, Carbon Steel, Nickel-plated Brass, etc. |
Valve Seal | Viton, EPDM, Nitrile, PTFE (Teflon), etc. |
Bolts/Nuts | Stainless Steel, Carbon Steel, Brass, etc. |
Gaskets | PTFE (Teflon), Graphite, Rubber, etc. |