DN50 Electric Globe Control Valves
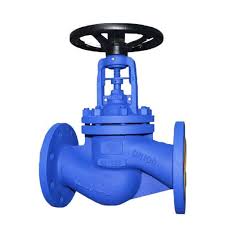
The Application of Electric Control Valve
Introducing Cameron‘s cutting-edge solutions in electric control valves, including globe valve control and globe control valves. These valves excel in regulating fluid flow with precision and reliability, making them indispensable in various industries. Cameron‘s electric control valves offer seamless integration into automation systems, ensuring optimal performance in applications such as HVAC, water treatment, and industrial processes. Trust Cameron for superior quality and efficiency in fluid control solutions.
What Are The Types Of Electric Control Valve?
- Electric Globe Control Valve: These valves feature a globe-shaped body and a linear motion mechanism for precise flow control. They are commonly used in applications requiring accurate regulation of flow rate and pressure.
- Electric Butterfly Control Valve: Butterfly valves use a disc or plate to control flow. Electric butterfly control valves are suitable for large flow applications and offer quick operation.
- Electric Ball Control Valve: Ball valves use a spherical disc to regulate flow. Electric ball control valves are versatile and suitable for a wide range of applications due to their reliable sealing and fast response.
- Electric Plug Control Valve: Plug valves use a cylindrical or tapered plug to control flow. Electric plug control valves are ideal for applications requiring tight shut-off and precise flow control.
- Electric Diaphragm Control Valve: Diaphragm valves use a flexible diaphragm to regulate flow. Electric diaphragm control valves are suitable for applications requiring corrosion resistance and sanitary conditions.
What Is Electric Control Valve?
An electric control valve is a type of valve that utilizes an electric actuator to regulate the flow of fluids in a system. It offers precise control over flow rate, pressure, and temperature, making it suitable for various industrial, commercial, and residential applications. Electric control valves are commonly used in HVAC systems, water treatment plants, chemical processing, and oil and gas industries, providing efficient and automated fluid control solutions.
How to Select the Right Electric Control Valve?
Selecting the right electric control valve involves considering factors such as the type of fluid, flow rate, pressure, temperature range, and system compatibility. Evaluate the specific requirements of your application and choose a valve that meets these criteria while ensuring reliable performance and longevity. Additionally, consult with industry experts or manufacturers to ensure optimal selection and integration into your system.
Features of Electric Control Valve
- Precision Control: Offers precise regulation of fluid flow, pressure, and temperature, ensuring accurate system performance.
- Automation: Allows for automated operation and integration into control systems, reducing manual intervention and enhancing efficiency.
- Versatility: Available in various types (e.g., globe, butterfly, ball), materials, and sizes to suit diverse applications and requirements.
- Remote Operation: Enables remote monitoring and control, providing flexibility and convenience.
- Fast Response: Provides rapid response to control signals, allowing for quick adjustments to changing process conditions.
- Durability: Constructed from durable materials such as stainless steel or brass, ensuring longevity and reliability.
- Wide Range: Offers a wide range of flow rates, pressure ratings, and temperature capabilities to accommodate different system demands.
- Low Maintenance: Requires minimal maintenance due to robust construction and fewer moving parts.
- Customization: Can be customized with accessories such as positioners or feedback devices to enhance functionality and performance.
- Energy Efficiency: Optimizes fluid flow and system operation, contributing to energy-efficient processes and reduced operational costs.
Advantages and Disadvantages of Electric Control Valve
Advantages:
- Precision Control: Allows for precise regulation of fluid flow, pressure, and temperature.
- Automation: Enables automated operation and integration into control systems, reducing manual intervention.
- Versatility: Available in various types, sizes, and materials to suit diverse applications.
- Remote Operation: Allows for remote monitoring and control, providing flexibility and convenience.
- Fast Response: Provides rapid response to control signals, facilitating quick adjustments.
- Durability: Constructed from durable materials, ensuring longevity and reliability.
- Wide Range: Offers a wide range of flow rates, pressure ratings, and temperature capabilities.
- Low Maintenance: Requires minimal maintenance due to robust construction and fewer moving parts.
Disadvantages:
- Initial Cost: Typically has a higher initial investment compared to manual valves.
- Complexity: Requires expertise for installation, setup, and maintenance.
- Dependence on Power: Relies on electricity for operation, making it susceptible to power outages.
- Potential Failure: May experience issues with electronic components, leading to downtime.
- Compatibility: Compatibility with existing systems and control infrastructure may be a consideration.
- Limited Response Time: Response time may be affected by system latency or communication delays.
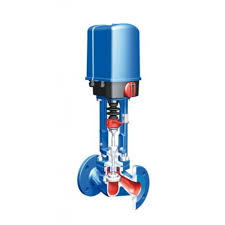
The Specifications of Electric Control Valve
Specification | Details |
---|---|
Type | Electric Control Valve |
Ball Material | Stainless Steel |
Attachment Type | Flanged |
Thread Standard | N/A |
Thread Size | N/A |
Body Material | Brass |
Safe for Use With | Water, HVAC fluids, chemicals |
Handle Type | Electric actuator |
Handle Material | N/A |
Maximum Working Pressure | 150 psi |
Maximum Working Pressure | 10.3 bar |
Operating Pressure | 5-100 psi |
The Installation Steps for Electric Control Valve
- Preparation:
- Gather all necessary tools and equipment, including wrenches, pipe tape, and a pipe cutter.
- Ensure the work area is clean and free from debris.
- Shut Off Utilities:
- Turn off the main power supply to the system to prevent accidental activation during installation.
- Close the valves on both the inlet and outlet lines.
- Positioning:
- Identify the optimal location for the valve installation based on system requirements and accessibility.
- Ensure sufficient space around the valve for maintenance and future adjustments.
- Pipe Preparation:
- Cut the pipes to the required length using a pipe cutter.
- Remove any burrs or debris from the pipe ends using a deburring tool.
- Attachment:
- Attach the valve to the existing piping system using appropriate fittings and connectors.
- Ensure proper alignment and secure attachment to prevent leaks.
- Sealing:
- Apply pipe tape or thread sealant to the threaded connections to ensure a tight seal.
- Tighten the connections using wrenches to the manufacturer’s recommended torque specifications.
- Electrical Connection:
- Connect the electric actuator of the valve to the control system using the provided wiring.
- Follow the manufacturer’s instructions for wiring connections and polarity.
- Testing:
- Open the main water supply valves.
- Gradually increase the power supply to the valve and test its operation.
- Check for leaks and ensure proper functioning of the valve in controlling fluid flow.
- Adjustment:
- Fine-tune the valve settings as necessary to achieve the desired flow rate and system conditions.
- Adjust the actuator position or control system settings according to system requirements.
- Final Inspection:
- Inspect the installation for any signs of leaks, loose connections, or other issues.
- Ensure all components are securely fastened and properly aligned.
- Confirm that the valve is operating correctly and meeting the desired performance criteria.
The Operation Theory of Electric Control Valve
- Electric Actuation: Electric control valves are equipped with an electric actuator that receives signals from a control system or operator. This actuator translates electrical signals into mechanical motion to adjust the valve’s position.
- Fluid Flow Regulation: Depending on the valve type and design, the electric actuator moves internal components such as a ball, plug, or disc to control the flow of fluid through the valve. For example, in 2-way globe control valves, the actuator adjusts the position of a plug or disc to regulate the flow of fluid between two ports.
- 3-Way Globe Control Valves: In 3-way globe control valves, the electric actuator controls the flow of fluid between three ports, allowing for more complex flow control configurations. These valves are commonly used in applications requiring mixing or diverting of fluids.
- Feedback Mechanism: Advanced electric control valves may incorporate feedback mechanisms such as position sensors or flow meters. These sensors provide real-time information about the valve’s position or the flow rate of the fluid, allowing the control system to make adjustments as needed to maintain desired process conditions.
- Automation and Integration: Electric control valves offer automation capabilities, allowing for seamless integration into control systems. This enables remote monitoring and control, as well as the implementation of complex control strategies for optimal system performance.