Characteristics and Kinds of Globe Valves – Angle Globe Valve | ZECO Valvevalves in oil and gas
genebre butterfly valve texas city
relient butterfly valve texas
4 butterfly valve
Table of Contents
- Flow Characteristics of Globe Valve
- 1. Needle globe valve
- Features of Needle Globe Valve
- How are Needle Valve and Globe Valve Different?
- 2. DC globe valve
- 3. Angle globe valve
- Classification of Angle Globe Valve
- How does an angle globe valve work?
- 4. Steel-ball or porcelain-ball sealed globe valve
- 5. High-temperature and high-pressure power station globe valve
- 6. Fluorine lined globe valve
- 7. Insulation globe valve
- 8. Electric flange globe valve
- 9. API stop valve
- 10. Stop valve for oxygen pipeline
- 11. Petroleum liquefied gas stop valve
- 12. Upper threaded stem globe valve
- 13. Lower threaded stem globe valve
- 14. API602 forged steel globe valve
- 15. Plunger globe valve
- 16. Bellows globe valve
- 17. Direct globe valve
Flow Characteristics of Globe Valve
The opening and closing parts of the stop valve (globe valve) are plug-shaped discs, their sealing surface is flat or conical, and the discs move linearly along the center line of the fluid. For valve stem movement, there are lifting rod types (the valve rod is raised and lowered, and the hand wheel does not rise and fall) and lifting and rotating lever types (the hand wheel and the valve stem are rotated and raised together, and the nut is provided on the valve body). The globe valve is only suitable for full opening and full close. It is not allowed for adjustment and throttling.
All globe valves have an inherent flow characteristic that defines the relationship between ‘valve opening’ and flow rate under constant pressure conditions. Please note that ‘valve opening’ in this context refers to the relative position of the valve plug to its closed position against the valve seat. It does not refer to the orifice pass area. The orifice pass area is sometimes called the ‘valve throat’ and is the narrowest point between the valve plug and seat through which the fluid passes at any time. For any valve, however, it is characterized, by the relationship between flowrate and orifice pass area is always directly proportional.
Valves of any size or inherent flow characteristic which are subjected to the same volumetric flow rate and differential pressure will have exactly the same orifice pass area. However, different valve characteristics will give different ‘valve openings’ for the same pass area. Comparing linear and equal percentage valves, a linear valve might have a 25% valve opening for a certain pressure drop and flow rate, whilst an equal percentage valve might have a 65% valve opening for exactly the same conditions. The orifice pass areas will be the same.
1. Needle globe valve
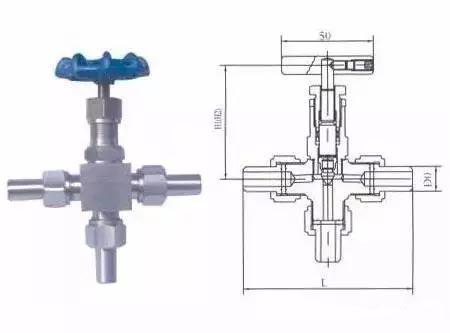
It is used for precise flow control. The valve disc is usually integrated into the valve stem, and it has a needle makeup head that cooperates with the valve seat with high accuracy. In addition, the thread pitch of the needle-type globe valve stem thread is smaller than that of the ordinary valve. Under normal circumstances, the size of the needle seat valve seat hole is smaller than the size of the pipe. Therefore, it is usually limited to pipelines with small nominal diameters and is more commonly used for sampling valves.
Features of Needle Globe Valve
- A compact but extremely sturdy design for high-pressure-temperature service.
- Available types: Stop, Stop check, Needle, and Flow control.
- Available with bolted or welded bonnet.
- Packing rings are precompressed to 4000 psi to provide a high-integrity seal.
- Repairable 2-piece stem drive.
- Available with double packing, leak-off connection, and live-loading.
How are Needle Valve and Globe Valve Different?
BASIS OF DIFFERENCE | NEEDLE VALVE | GLOBE VALVE |
PURPOSE | A needle valve is used where continuous throttling is required to regulate a flow. | A globe butterfly valve is used where a flow is needed for flow control or throttling. |
PLUG SHAPE | A needle valve features a needle-shaped plug. | A globe valve features a disc-shaped plug. |
SIZE | The size of a needle valve is smaller than a globe valve. | The size of a globe valve is more significant than a needle valve. |
APPLICATION | It is helpful in precision equipment as it offers an outstanding level of flow control. | A wholesale actuated globe valve is helpful in operations requiring frequent opening and closing. |
INDUSTRIES | It is used in gas bleeder lines, analog field instruments, metering applications, automated combustion control systems, and pressure pump governors. | It is used in water cooling, fuel oil, drain, chemical feed, feedwater, control valve bypass, oil and gas, refinery, air condenser extraction, and boiler vent systems. |
2. DC globe valve
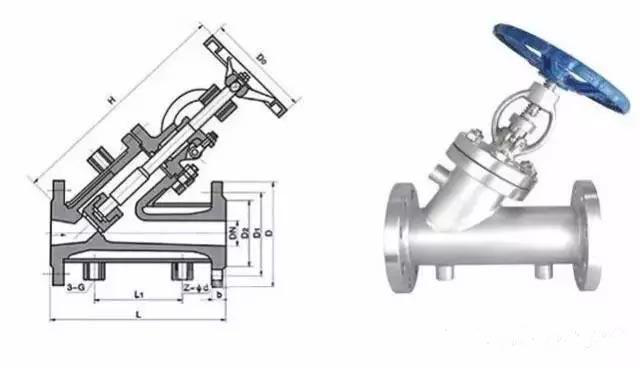
The stem and channel of the DC-type globe valve form a certain angle, and the sealing surface of the valve seat and the inlet and outlet passage also has a certain angle. The valve body can be made integral or separated. The globe valve that has a separate valve body uses two valve bodies to sandwich the valve seat in the middle for easy maintenance. This type of stop valve allows the fluid to hardly change the flow direction, and the flow resistance is minimized in the globe valve. The sealing surface of the valve seat and valve disc can be welded with hard alloy to make the entire valve more resistant to erosion and corrosion, which is very suitable for pipeline control in the alumina production process, and it is also suitable for pipelines with coke and solid particles.
3. Angle globe valve
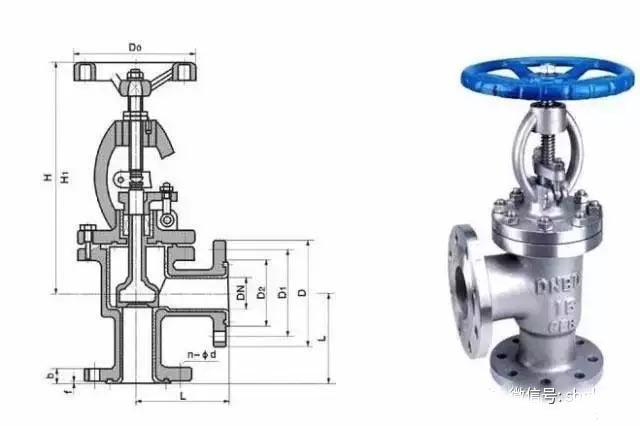
The biggest advantage of the angle globe valve is that the valve can be installed at the corner of the piping system, which is easy to operate and not necessary to use 90 ° elbow. Therefore, this type of valve is most suitable to be used in synthetic ammonia production systems and refrigeration systems in fertilizer plants. For example, J44H-160, J44H-320, L44H-160, and L44H-320 are completely designed for synthetic ammonia production systems.
Classification of Angle Globe Valve
These valves can be classified depending on various parameters:
- Design of Valve Disc: Conventional or Ball disc, Composition disc, and Plug type disc.
- Disc–Stem configurations of Valve: Rotating Stem with Integral or Non-Integral Disc and Non-Rotating Stem with Integral Disc or Non-Integral Disc.
- Valve Stem Screw: Inside and Outside stem screw.
- Bonnet Design of Valve: Bolted Bonnet, Welded Bonnet, Flanged Bonnet, Union ring Bonnet, and Pressure seal Bonnet
How does an angle globe valve work?
The angle globe valve’s opening and closing sections are plug-shaped valve discs, the sealing surface is smooth or conical, and the flap travels linearly down the fluid’s centerline. The inlet and outlet channels of an angle globe valve, also known as an angle valve, are not in the same direction, creating a 90° right angle. This form of globe valve allows the medium flowing through it to change its flow path, resulting in a pressure drop.
4. Steel-ball or porcelain-ball sealed globe valve
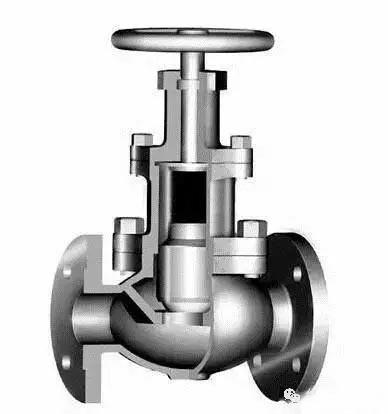
The structural feature of the valve is that the valve body is divided into one-piece type and split type. The valve disc is a STL hard alloy steel ball, or a ceramic ball made of amorphous material by powder forming, high temperature sintering and fine development. The rolling envelope ball at the lower end of the valve stem is inside the valve hole. When the ball is rotated three-dimensionally in the ball hole of the valve stem, countless seal lines can be generated, which increases the service life of the sealing surface and can also ensure a reliable sealing.
Due to the limitation of the ball seal, this valve is generally used for smaller nominal passages, about 6-25mm. The valve is suitable for high-temperature and high-pressure steam pipelines in nuclear power plants and thermal power plants, instrumentation pipelines for sampling and sewage systems, and temperature-resistant, pressure-resistant, wear-resistant and corrosion-resistant pipelines in petrochemical and chemical systems.
5. High-temperature and high-pressure power station globe valve
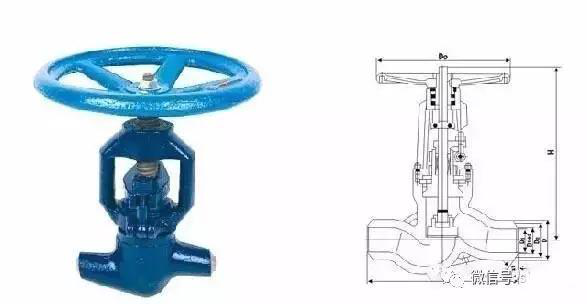
The structural feature of the valve is that the connection between the valve body and the valve cover adopts a pressure self-tight seal type or a clamp type. The connection form of the valve body and the pipeline is a butt welding connection. The material of the valve body is mostly chrome molybdenum steel or chrome molybdenum vanadium steel, and the sealing surface is mostly welded with hard alloy.
Therefore, this type of valve is resistant to high temperature and pressure with good heat resistance; the sealing surface is resistant to wear, abrasion, corrosion, and it has good sealing performance and long life. It is most suitable for high-temperature and high-pressure and superheated steam pipelines in thermal power industry systems, petrochemical systems and metallurgy.
6. Fluorine lined globe valve
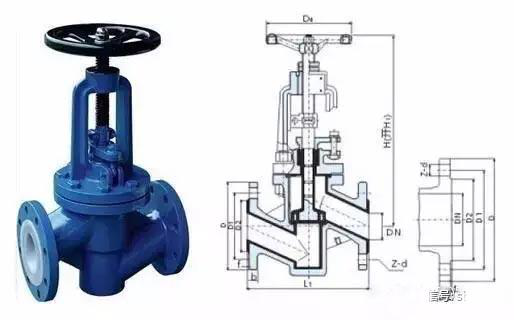
The opening and closing member of the fluorine-lined globe valve is a plug-shaped disc. The sealing surface is flat or conical, and the valve flap moves linearly along the center line of the fluid. For the movement form of the valve stem, there are lifting rod type (the valve rod is raised and lowered, and the hand wheel does not rise and fall) and lifting rotating rod type (the hand wheel and the valve rod are rotated and raised together, and the nut is provided on the valve body).
The globe valve is only suitable for full open and full close. It is not allowed to used for adjustment and throttling. The fluorine-lined stop valves is suitable for aqua regia, sulfuric acid, hydrochloric acid, hydrofluoric acid, and various organic acids, strong acids and strong oxidants at -50 to 150 ° C. It is also suitable for various concentrations of strong alkali organic solvents and other corrosive gas and liquid medium pipelines.
7. Insulation globe valve
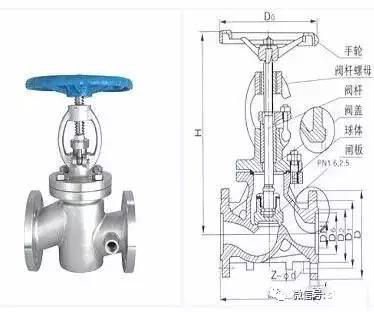
The opening and closing piece of the insulation glo valve is a plug-shaped disc. The sealing surface is flat or conical, and the valve flap moves linearly along the center line of the fluid. For the movement form of the valve stem, there are lifting rod type (the valve rod is raised and lowered, and the hand wheel does not rise and fall) and lifting rotating rod type (the hand wheel and the valve rod are rotated and raised together, and the nut is provided on the valve body).
The corrugated globe valve is only suitable for full open and full close, and it is not allowed to be used for adjustment and throttling. The insulation globe valve is mainly used in petroleum, chemical, metallurgy, pharmaceutical and other systems to transport high-viscosity media that will solidify at room temperature. The insulation jacket of the DC jacket insulation globe valve is welded between the two flanges of the valve, and two connection ports of the insulation jacket are provided on the side and bottom of the valve. The DC insulation globe valve is particularly suitable for pipelines in the chemical and fertilizer industries. The steam contained in the jacket can prevent the medium from crystallization. Insulated globe valves are widely used in various systems such as petroleum, chemical, metallurgy and pharmaceuticals.
8. Electric flange globe valve
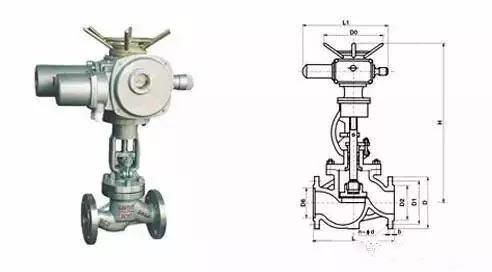
Electric flange globe valve and flange gate valve is the same type of valve. It consists of electric actuator or pneumatic actuator and shut-off valve. The difference is that the closing part of the electric flange globe valve is a valve body. The valve body is rotated around the center line of itself to open and close the valve.
The gate valve is mainly used to cut off, distribute and change the flow direction of the medium in the pipeline. It has a wide range of applications, from several millimeters to large meters, and can be applied from high vacuum to high pressure.
9. API stop valve
This type of globe valve is designed in strict accordance with the ASMEB16.34 standard; the connection between the valve body and the bonnet, the stuffing box, the installation of the stem nut, and the upper seal are all designed in strict accordance with API600. The valve material fully meets the requirements of API600. Its structural length conforms to ASMEB16.10; flange connection dimensions conform to ANSI / ASMEB16.5a. The inspection and test of the valve is carried out strictly in accordance with API598. Therefore, the valve is widely used in petrochemical pipelines, and it is also suitable to be used in power, metallurgy, textile and other systems.
10. Stop valve for oxygen pipeline
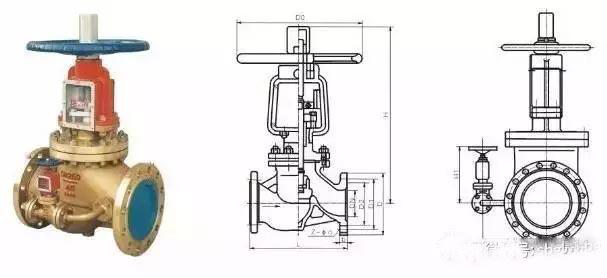
11. Petroleum liquefied gas stop valve
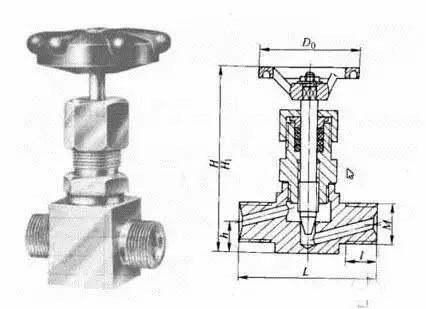
This valve is specially designed for the pipeline or device of petroleum liquefied gas, focusing on the fire protection requirements in structure. The packing is made of polytetrafluoroethylene, which has a reliable sealing and never leaks. The sealing sub-material is made of polytetrafluoroethylene or nylon on the valve body, which is soft and reliable. This valve is suitable for the liquefied petroleum gas pipeline system as an opening and closing device, and also suitable for other pipelines with a temperature ≤80 ° C.
12. Upper threaded stem globe valve
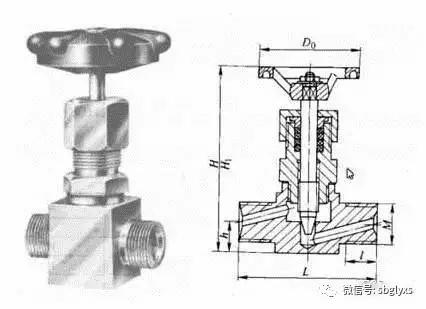
Upper threaded stem globe valve: the thread of the stem of the globe valve is outside the valve body. The advantage is that the valve stem is not affected by the medium and is easy to lubricate. This kind of structure is commonly used.
The stem of this type of stop valve does not directly contact the working medium. It is suitable for different working conditions according to the different materials of the casing, the material of the sealing pair, the material of the packing and the material of the valve stem. If the material of the valve body and valve cover is carbon steel, the sealing sub-material is alloy steel, the filler is flexible graphite, and the material of the valve stem is Cr13 series stainless steel, which is suitable for water, steam and oil pipelines. If the valve body and bonnet material are 1Cr18Ni9 or 0Cr18Ni9, the sealing sub-material is the valve body material or hard alloy, the filler is polytetrafluoroethylene, and the valve stem material is Cr17Ni2, which is suitable for corrosive medium pipeline and device based on nitric acid. However, the maximum nominal through diameter of this type of stop valve is 200mm, and a bypass valve or an internal bypass structure should be provided on the stop valve above 200. Generally, the inlet end of a DN ≥200mm globe valve is above the valve disc, that is, high in and low out. This is to prevent from using great effort when closing it and a thick stem.
13. Lower threaded stem globe valve
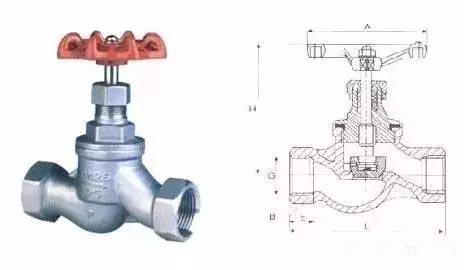
Lower threaded stem globe valve: the thread of the globe valve stem is in the valve body. This structure of the valve stem thread directly contacts with the medium, susceptible to erosion, and cannot be lubricated. This structure is used in places with small diameter and low temperature.
The stem thread of this type of globe valve is in direct contact with the working medium and directly eroded by the medium, which makes the stem thread susceptible to rust and causes laborious opening and closing. The globe valve in this structure has a relatively small nominal passage, generally between 6 and 50 mm, and is mostly used for instrument valves and sampling valves.
14. API602 forged steel globe valve
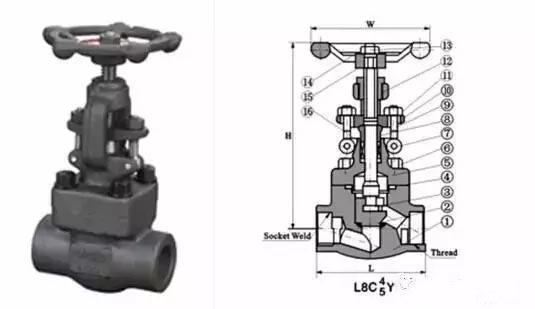
This type of globe valve is designed according to American Petroleum Institute standard API602. The body and bonnet are forged from carbon steel or stainless steel. The valve body and the bonnet are connected with a bolt connection, a screw connection and welding, and are divided into an upper threaded stem and a lower threaded stem. The sealing sub-material is Cr13 steel, stainless steel acid steel to STL hard alloy. The filler is flexible graphite or polytetrafluoroethylene. Connection methods include flange, thread, socket welding and butt welding. The pressure level is CL150 ~ CL1500, and the nominal pass is 1/4 ~ 2in.
This type of globe valve is widely used in the equipment and pipelines of petrochemical, power, chemical and other departments. The working medium is steam, oil, and corrosive media. The structure length is according to ASMEB16.10, the flange connection size is according to ASME / ANSIB16.5a, the welding end size is in accordance with ASMEB16.25, the socket welding hole size is in accordance with ANSIB16.11, and the screw connection end size is in accordance with ANSIB1.20.1.
15. Plunger globe valve
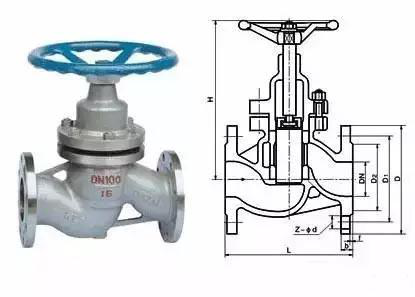
This type of plunger valve is a radial seal, which is realized by two elastic sealing rings sleeved on the polished plunger. The two elastic sealing rings are separated by a collar, and the elastic sealing ring around the plunger is pressed firmly by the load applied to the valve cover by the valve body and the valve cover connecting bolts to ensure the seal. The material of the valve is composed of carbon steel for the housing and Cr13 stainless steel for the plunger. Flexible graphite for sealing ring can be used for water, steam and oil pipelines. If the shell is made of stainless acid-resistant steel, the plunger is made of stainless acid-resistant steel, and the sealing ring is made of polytetrafluoroethylene, which is suitable for acid and alkali corrosive media.
The valve has the advantages of reliable sealing, long life and easy maintenance; the disadvantage is slow opening and closing speed. This type of valve is widely used in urban construction systems, water and steam pipelines in urban heating system.
16. Bellows globe valve
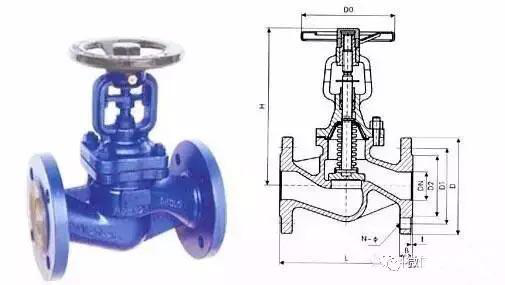
The bellows globe valve is also called a bellows sealed globe valve. Through automatic roll welding, a metal barrier is formed between the fluid medium and the atmosphere to ensure a zero leakage design of the valve stem. The bellows globe valve uses a bellows structure inside, and the lower end of the stainless steel bellows is welded to the valve stem to prevent the process fluid from eroding the valve stem. The other end is placed between the valve body and the valve cover to form a static seal. For dual seal design, if the bellows fails, the valve stem packing will also prevent leakage. The corrugated pipe welding and the valve stem maintain stable running performance to avoid valve stem vibration caused by valve plug vibration. It is most suitable for pipelines of steam, flammable, explosive, thermal oil, high purity, toxic and other media.
17. Direct globe valve
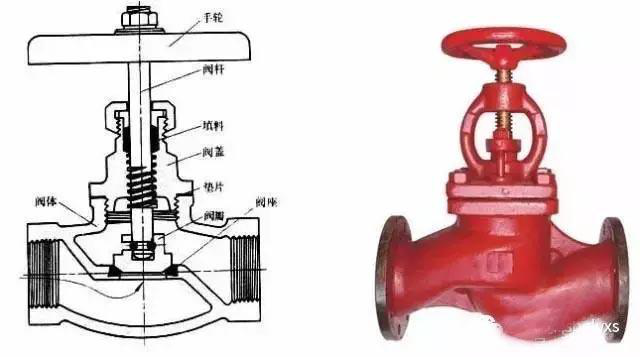
The inlet and outlet channels of media of the straight stop valve are in the same direction at 180 °. This type of globe valve has relatively small damage on the flow state, so the pressure loss through the valve is correspondingly reduced. It relies on the pressure of the valve stem to tightly combine the sealing surface of the valve disc with the sealing surface of the valve seat to prevent the medium from flowing. During the opening and closing process, the friction between the sealing surfaces is small, wear-resistant, the opening height is small, and the manufacturing process performance is good. Compared with gate valves, globe valves have a simpler structure and are more convenient to be manufactured and maintained. It is the most widely-used valve in the industrial sector.
Related Tags :
ZECO Valve
What is a Gate Valve?
Shanghai Pressure Reducing Valve Factory
Gate Valve vs Ball Valve
What is an Axial Check Valve
Difference Between Gate Valve And Butterfly Valve
What is a Globe Valve?
What are Globe Valves?