DN50 150LB Motorized Control Valve

The Application of Motorized Control Valve
Introducing Motorized Control Valve solutions by Cameron – ideal for precise flow control in various applications. Whether it’s an air motor control valve regulating airflow in industrial systems or an EGR valve control solenoid motor managing exhaust gas recirculation, our innovative solutions offer reliability and efficiency. Trust Cameron for advanced motorized valves tailored to your specific needs.
What Are The Types Of Motorized Control Valve?
- Electric Motorized Control Valve: Actuated by an electric motor, providing precise control over flow rates with smooth and continuous operation.
- Pneumatic Motorized Control Valve: Utilizes pneumatic power to actuate the valve, suitable for applications where compressed air is readily available.
- Hydraulic Motorized Control Valve: Actuated by a hydraulic motor, offering robust performance and high torque for demanding applications.
- Solenoid Motorized Control Valve: Features a solenoid motor for quick and precise control, commonly used in applications requiring rapid response times.
- Combination Motorized Control Valve: Integrates multiple control mechanisms, such as electric and pneumatic, to provide versatile control options for complex systems.
What Is Motorized Control Valve?
A Motorized Control Valve is a type of valve equipped with an electric, pneumatic, hydraulic, or solenoid motor for automated operation. It regulates fluid flow by adjusting the position of the valve plug, disk, or ball in response to control signals. This enables precise and remote control over flow rates, pressure, or temperature in various industrial processes, HVAC systems, and fluid handling applications, enhancing efficiency and accuracy.
How to Select the Right Motorized Control Valve?
Selecting the right Motorized Control Valve involves considering factors such as flow requirements, pressure ratings, media compatibility, and control system integration. Determine the appropriate actuation type—electric, pneumatic, hydraulic, or solenoid—based on application needs and available resources. Consult with experts to ensure the valve’s specifications align with the system requirements for optimal performance and reliability.
Features of Motorized Control Valve
- Precise Control: Motorized Control Valves offer precise regulation of flow rates, allowing for accurate adjustment to meet specific process requirements.
- Remote Operation: Equipped with motors, these valves can be operated remotely, enabling integration into automated systems and facilitating remote monitoring and control.
- Versatility: Available in various actuation types, including electric, pneumatic, hydraulic, and solenoid, to suit different application needs and preferences.
- Quick Response: Motorized valves provide rapid response times, enabling swift adjustments to changing process conditions for enhanced efficiency.
- Integration: These valves can easily integrate with control systems and automation platforms, allowing for seamless communication and coordination within the overall system.
- Reliability: Designed for robust performance, Motorized Control Valves offer reliable operation even in demanding industrial environments, minimizing downtime and maintenance requirements.
Advantages and Disadvantages of Motorized Control Valve
Advantages:
- Precision: Motorized Control Valves offer precise control over flow rates, pressure, or temperature, ensuring accurate regulation in various applications.
- Automation: Automation capabilities enable remote operation and integration into control systems, reducing manual intervention and enhancing efficiency.
- Versatility: Available in different actuation types, Motorized Control Valves can accommodate diverse application requirements and preferences.
- Quick Response: These valves provide rapid response times, facilitating immediate adjustments to changing process conditions for optimal performance.
Disadvantages:
- Initial Cost: The initial investment for Motorized Control Valves may be higher compared to manually operated valves due to the inclusion of motors and automation components.
- Complexity: The integration of motors and automation systems adds complexity to the valve design, potentially increasing maintenance requirements and costs.
- Dependence on Power: Operation of Motorized Control Valves is dependent on a power source, making them vulnerable to power outages or electrical failures.
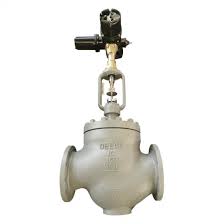
The Specifications of Motorized Control Valve
Specification | Details |
---|---|
Type | Motorized Control Valve |
Ball Material | Stainless Steel, Brass, PTFE, or others |
Attachment Type | Flanged, Threaded, Socket Weld, or others |
Thread Standard | ANSI, DIN, JIS, BSP, or others |
Thread Size | 1/2 inch to 24 inches |
Body Material | Cast Iron, Carbon Steel, Stainless Steel, or others |
Safe for Use With | Water, Oil, Gas, Steam, Chemicals, etc. |
Handle Type | Electric Actuator |
Handle Material | Stainless Steel, Aluminum, or Composite |
Maximum Working Pressure | Up to 1500 psi (103.42 bar) |
Maximum Working Pressure | Up to 103.42 bar |
Operating Pressure | Typically 0-300 psi (0-20.68 bar) |
The Installation Steps for Motorized Control Valve
- Prepare Work Area: Clear the installation area, ensuring there is ample space to work around the valve and associated piping.
- Shut Off Supply: Turn off the main supply of fluid (water, gas, etc.) to the system where the valve will be installed.
- Relieve Pressure: Release any pressure in the system by opening nearby valves or faucets and draining any residual fluid.
- Select Location: Choose a suitable location for installing the valve, considering factors such as accessibility and alignment with the piping system.
- Prepare Pipes: Clean and deburr the ends of the pipes where the valve will be connected to ensure a proper seal.
- Mount Valve: Securely mount the Motorized Control Valve to the piping system using the appropriate attachment type (flanged, threaded, etc.).
- Connect Pipes: Attach the pipes to the valve using suitable connectors and fittings, ensuring tight connections.
- Wiring: Connect the electrical wiring to the valve’s electric actuator according to the manufacturer’s instructions, ensuring proper polarity and grounding.
- Test Connections: Test all connections for leaks by pressurizing the system and inspecting for any signs of leakage.
- Power Up: Apply power to the electric actuator and verify that the valve operates correctly in response to control signals.
- Final Checks: Perform a final inspection of the installation to ensure everything is properly aligned, secured, and functioning as intended.
The Operation Theory of Motorized Control Valve
- Actuation Mechanism: Motorized Control Valves utilize an electric, pneumatic, hydraulic, or solenoid motor to regulate the flow of fluid through the valve.
- Position Control: The motorized actuator precisely adjusts the position of the valve’s internal components, such as a plug, ball, or disc, to modulate the flow rate.
- Control Signals: Control signals, typically generated by a control system or operator, dictate the desired position of the valve. The motorized actuator responds to these signals to achieve the specified flow control.
- Feedback Mechanism: Many Motorized Control Valves incorporate feedback mechanisms to provide information on the valve’s position and performance. This feedback allows for accurate monitoring and adjustment of the valve’s operation.
- Integration: Motorized Control Valves can be seamlessly integrated into control systems, allowing for remote operation, automation, and coordination with other components in the system.
Hydraulic Motor Flow Control Valve
- Hydraulic Actuation: Hydraulic Motor Flow Control Valves use hydraulic pressure to actuate the valve, offering robust performance and high torque for precise flow control.
- Flow Regulation: These valves regulate fluid flow by adjusting the size of the valve opening in response to changes in hydraulic pressure, providing accurate control over flow rates.
- Versatility: Hydraulic Motor Flow Control Valves are suitable for a wide range of applications, including industrial processes, agricultural machinery, and construction equipment, where precise flow control is essential.
- Reliability: With fewer moving parts and robust construction, hydraulic valves offer reliable operation even in harsh environments, minimizing downtime and maintenance requirements.