Pinch Valve
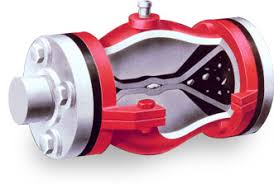
The Application of Pinch Valve
Cameron, a renowned manufacturer of industrial valves, offers a wide range of solutions, including the versatile pinch valve. Designed to excel in diverse applications, the pinch valve is particularly well-suited for handling corrosive fluids and gases. Unlike traditional stainless steel swing check valves or stainless steel ball check valves, the pinch valve operates by constricting the pipe, effectively sealing off the flow. This unique mechanism makes the pinch valve an ideal choice for applications involving check valve stainless steel components, where reliable shut-off and leak prevention are of utmost importance, such as in the chemical, petrochemical, and power generation industries. Cameron’s innovative pinch valve technology combines durable construction, precise control, and enhanced safety, making it a preferred solution for demanding fluid handling requirements.
What Are The Types Of Pinch Valve?
- Pneumatic Pinch Valves:
- Actuated by compressed air or gas to open and close the valve.
- Offer precise control and fast response times.
- Commonly used in automated process control applications.
- Manual Pinch Valves:
- Operated manually using a lever or handwheel.
- Provide simple and affordable flow control.
- Suitable for occasional or infrequent adjustments.
- Electro-Pneumatic Pinch Valves:
- Combine electric actuation with pneumatic control.
- Allow remote operation and integration with control systems.
- Offer advanced functionality and programmable control.
- Sleeved Pinch Valves:
- Feature a flexible sleeve or diaphragm that pinches the pipe.
- Provide tight shut-off and can handle abrasive or corrosive media.
- Suitable for applications with high pressure or temperature requirements.
- Knife-Edge Pinch Valves:
- Use a sharp metal edge to pinch and seal the pipe.
- Designed for reliable shut-off, even with high-viscosity fluids.
- Commonly used in food, pharmaceutical, and chemical industries.
What Is Pinch Valve?
A pinch valve is a type of industrial valve that controls the flow of fluids, gases, or slurries by physically constricting or “pinching” the pipe or hose in which the medium is flowing. Unlike traditional valves that use a moving part, such as a ball or gate, to regulate the flow, a pinch valve works by compressing the pipe, effectively sealing off the passage and stopping the flow. This unique design makes pinch valves particularly well-suited for handling abrasive, corrosive, or viscous materials, as there are no internal moving parts that can be damaged or worn down over time. The ability to provide tight shut-off and zero leakage makes pinch valves a popular choice in a wide range of industrial applications, including chemical processing, mining, wastewater treatment, and more.
How to Select the Right Pinch Valve?
Flow Rate: Determine the required flow rate and choose a pinch valve with the appropriate size and design to handle the necessary volume.
Pressure Rating: Ensure the pinch valve can withstand the maximum operating pressure of the system without leakage or failure.
Material Compatibility: Select materials, such as elastomers and wetted components, that are compatible with the fluid or gas being controlled to prevent corrosion or chemical attack.
Actuation Method: Choose between manual, pneumatic, or electric actuation based on the level of control and automation required.
Installation Requirements: Consider the available space, pipe configuration, and accessibility to determine the appropriate pinch valve style and orientation.
By carefully evaluating these key criteria, users can select the most suitable pinch valve that will provide reliable, long-lasting performance in their specific application.
Features of Pinch Valve
Tight Shut-Off:
Pinch valves are designed to provide a tight, leak-free seal when closed, preventing any backflow or fluid leakage.
Abrasion Resistance:
The unique pinching mechanism and use of durable materials make pinch valves highly resistant to wear and abrasion, even when handling aggressive or particulate-laden media.
Corrosion Resistance:
Pinch valves can be constructed with corrosion-resistant materials, such as stainless steel or specialized elastomers, to withstand chemical attack and operate reliably in harsh environments.
Easy Maintenance:
With no internal moving parts, pinch valves typically require minimal maintenance and can be serviced quickly, reducing downtime and maintenance costs.
Versatile Actuation:
Pinch valves can be actuated manually, pneumatically, or electrically, providing flexibility in control and integration with automation systems.
Compact Design:
The simple, streamlined design of pinch valves allows for a smaller footprint and easier installation in space-constrained environments.
Advantages and Disadvantages of Pinch Valve
Advantages of Pinch Valves:
Zero Leakage: Pinch valves can provide a tight, leak-proof seal when closed, preventing any unwanted fluid or gas escape.
Handling of Abrasive/Corrosive Media: The pinching mechanism and use of durable materials make pinch valves well-suited for applications involving abrasive or corrosive substances.
Minimal Maintenance: With no internal moving parts, pinch valves require relatively low maintenance compared to other valve types.
Compact Design: The simple, streamlined design of pinch valves allows for a smaller footprint and easier installation in tight spaces.
Versatile Actuation: Pinch valves can be manually, pneumatically, or electrically actuated, providing flexibility in control and automation.
Disadvantages of Pinch Valves:
Limited Flow Capacity: Pinch valves may have a lower maximum flow capacity compared to other valve types, depending on the pipe size and valve design.
Potential for Pipe Damage: Repeated pinching action can potentially cause wear and damage to the pipe material over time, especially with softer or more flexible pipe materials.
Temperature Limitations: The performance of the elastomeric components in pinch valves may be affected by extreme temperatures, limiting their suitability for certain high or low-temperature applications.
Higher Initial Cost: Pinch valves can have a higher initial purchase cost compared to some other valve types, although the low maintenance requirements may offset this in the long run.
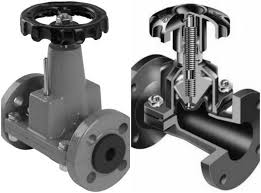
The Specifications of Pinch Valve
Specification | Details |
---|---|
Type | Pneumatic Pinch Valve |
Ball Material | N/A (Pinch Valve Design) |
Attachment Type | Flanged |
Thread Standard | N/A |
Thread Size | N/A |
Body Material | 316 Stainless Steel |
Safe for Use With | Corrosive, Abrasive, and High-Viscosity Fluids |
Handle Type | Pneumatic Actuator |
Handle Material | Aluminum |
Maximum Working Pressure | 150 psi |
Maximum Working Pressure | 10 bar |
Operating Pressure | 80-100 psi |
The Installation Steps for Pinch Valve
Site Preparation:
- Ensure the installation location has sufficient clearance for the valve and any associated piping or equipment.
- Verify that the pipeline is properly supported and aligned to prevent excessive stress on the valve.
Valve Orientation:
- Determine the optimal valve orientation based on the flow direction and accessibility requirements.
- Pinch valves can be installed in both horizontal and vertical pipe runs.
Pipe Preparation:
- Cut the pipe to the appropriate length to accommodate the valve’s dimensions.
- Ensure the pipe ends are clean, free of burrs, and properly aligned.
Valve Placement:
- Position the pinch valve at the desired location within the pipeline.
- Align the valve flanges or connections with the corresponding pipe flanges or connections.
Valve Securing:
- Secure the pinch valve in place using the appropriate fasteners, such as flange bolts.
- Tighten the fasteners in a star or cross pattern to ensure even distribution of the clamping force.
Pneumatic/Electrical Connections:
- If the pinch valve is pneumatically or electrically actuated, connect the appropriate air supply or electrical power source.
- Ensure all connections are properly made and tightened to prevent leaks or malfunctions.
Leak Testing:
- Perform a thorough leak test on the installed pinch valve and surrounding piping.
- Gradually increase the system pressure and check for any signs of leakage or failure.
Final Inspection:
- Verify that the pinch valve is functioning correctly, with smooth and consistent operation.
- Document the installation details and any relevant parameters for future reference.
The Operation Theory of Pinch Valve
Operation Theory of Pinch Valves:
Pinch valves work by using a compressive force to “pinch” the pipe or tubing, effectively closing off the flow path. This pinching action is typically achieved through the use of a pneumatic, electric, or manual actuator that applies pressure to the pipe, causing it to deform and seal. Unlike other valve types, pinch valves do not have any internal moving parts that come into contact with the fluid, making them well-suited for handling abrasive, corrosive, or viscous materials.
Onyx Pinch Valves:
Onyx Pinch Valves are a leading manufacturer of high-quality pinch valves for a wide range of industrial applications. Onyx Pinch Valves are known for their robust construction, tight shut-off capabilities, and excellent corrosion resistance. Their pinch valve designs feature durable elastomeric liners and reinforced bodies to withstand the most challenging operating conditions. Onyx Pinch Valves offer a variety of actuation options, including pneumatic, electric, and manual, to provide flexibility in control and integration with existing systems.
Pinch Valve Manufacturers:
In addition to Onyx Pinch Valves, there are several other prominent pinch valve manufacturers in the market, each offering their own unique features and capabilities. Some of the leading pinch valve manufacturers include:
- Wener Pinch Valves
- Red Valve Company
- Cla-Val
- Bray International
- SISTAG AG