Flanged Check Valve Swing Type
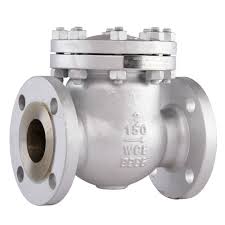
The Application of Flanged Check Valve
Cameron, a leading manufacturer of industrial valves, offers a range of high-quality stainless steel swing check valves and stainless steel ball check valves that are well-suited for a variety of applications, particularly in the chemical, petrochemical, and oil and gas industries. The flanged check valve design provides a secure and reliable method of preventing backflow, making it an essential component in process systems that require unidirectional fluid control. These stainless steel check valves are renowned for their exceptional corrosion resistance, durability, and ability to handle demanding operating conditions, making them a popular choice for applications involving aggressive media or harsh environments. Whether you require a stainless steel swing check valve or a stainless steel ball check valve, Cameron offers a diverse range of options to meet your specific requirements and ensure the safe and efficient operation of your fluid handling system.
What Are The Types Of Flanged Check Valve?
1. Stainless Steel Swing Check Valve:
- The valve disc is hinged and swings open to allow forward flow, then closes to prevent backflow.
- Commonly used in pipeline applications due to their simple and reliable design.
2. Stainless Steel Ball Check Valve:
- Utilizes a stainless steel ball that sits on the valve seat, opening to allow forward flow and closing to prevent backflow.
- Provides a tight seal and can handle higher pressures compared to swing check valves.
3. Stainless Steel Lift Check Valve:
- Features a guided disc that lifts off the seat to open the valve for forward flow.
- Suitable for applications requiring a smaller pressure drop across the valve.
4. Stainless Steel Dual Plate Check Valve:
- Uses two hinged plates that open to allow forward flow and close to prevent backflow.
- Offers high flow capacity and can handle rapid flow reversal.
5. Stainless Steel Wafer Check Valve:
- A compact design that can be installed between flanges in a pipeline.
- Ideal for space-constrained applications.
What Is Flanged Check Valve?
A flanged check valve is a type of valve designed to allow fluid flow in one direction while preventing backflow. The valve features a flanged connection, which provides a secure and leak-tight attachment to the piping system. The check valve mechanism, typically either a swing, ball, or lift design, opens to permit forward flow and automatically closes when the flow reverses direction, preventing the backflow of media. Flanged check valves are commonly used in applications where it is critical to maintain unidirectional flow, such as in pipelines, pumping systems, and industrial processes. The flanged design offers a robust and reliable solution for controlling fluid flow and ensuring the safety and integrity of the overall system.
How to Select the Right Flanged Check Valve?
Media Compatibility: Ensure the valve materials, such as the body and internal components, are compatible with the fluid or gas you will be handling. Stainless steel is a common choice for its corrosion resistance.
Pressure and Temperature Ratings: Match the valve’s pressure and temperature ratings to the operating conditions of your system to ensure safe and reliable performance.Flow Rate and Pressure Drop: Choose a valve size and design that can accommodate the required flow rate while minimizing pressure drop across the valve.Installation Requirements: Consider the available space, piping configuration, and accessibility requirements when selecting the appropriate flanged check valve design, such as a swing, ball, or lift check valve.Regulatory Compliance: Ensure the valve meets any relevant industry standards or regulations for your application, such as those related to safety or environmental protection.
Features of Flanged Check Valve
Easy Installation
Flanged check valves feature a flanged connection, which allows for simple and secure installation directly into the piping system.
Corrosion Resistance
The use of stainless steel and other corrosion-resistant materials in the construction of flanged check valves ensures their durability and suitability for harsh environments.
Tight Sealing
The valve’s precise design and tight-fitting components provide a reliable seal to prevent backflow, ensuring the integrity of the fluid handling system.
Versatility
Flanged check valves are available in a variety of configurations, such as swing, ball, and lift designs, allowing for flexibility in addressing different application requirements.
High Flow Capacity
Many flanged check valve models are engineered to offer a high flow capacity, making them suitable for applications with substantial fluid throughput.
Durable Construction
The robust, metal-to-metal construction of flanged check valves ensures long-lasting performance and resistance to wear, even in demanding operating conditions.
Advantages and Disadvantages of Flanged Check Valve
Advantages of Flanged Check Valve:
Secure Attachment: The flanged connection provides a strong and leak-tight attachment to the piping system, ensuring reliable operation.
Corrosion Resistance: The use of stainless steel and other corrosion-resistant materials enhances the valve’s durability and service life.
Tight Sealing: Flanged check valves offer a reliable seal to prevent backflow, maintaining the integrity of the fluid handling system.
Versatility: The availability of different design options, such as swing, ball, and lift check valves, allows for flexibility in addressing various application requirements.
High Flow Capacity: Many flanged check valve models are engineered to handle high flow rates, making them suitable for applications with substantial fluid throughput.
Disadvantages of Flanged Check Valve:
Installation Complexity: The flanged connection may require more complex installation compared to some other check valve types.
Limited Space: The flanged design can be relatively bulky, which may pose challenges in applications with limited available space.
Potential Leakage: If the flanged connection is not properly installed or maintained, there is a risk of potential leakage.
Higher Cost: Flanged check valves may have a higher initial cost compared to some other check valve types due to their more complex design and construction.
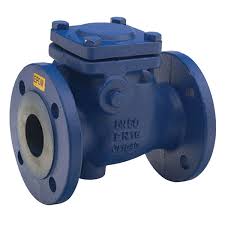
The Specifications of Flanged Check Valve
Specification | Value |
---|---|
Type | Stainless Steel Swing Check Valve |
Ball Material | N/A (Swing Disc Design) |
Attachment Type | Flanged |
Thread Standard | N/A |
Thread Size | N/A |
Body Material | ASTM A351 CF8M Stainless Steel |
Safe for Use With | Corrosive Fluids, Gases, and Chemicals |
Handle Type | N/A |
Handle Material | N/A |
Maximum Working Pressure | 285 psi (20 bar) |
Operating Pressure | 0-285 psi (0-20 bar) |
The Installation Steps for Flanged Check Valve
Step 1: Prepare the Piping System
- Ensure the piping system is clean and free of any debris or obstructions.
- Measure the exact distance between the two flanges where the check valve will be installed.
Step 2: Select the Appropriate Gaskets
- Choose gaskets that are compatible with the media and the operating conditions of your system.
- Verify that the gasket dimensions match the flange size and bolt pattern.
Step 3: Position the Check Valve
- Place the flanged check valve between the two mating flanges, ensuring proper alignment.
- Make sure the valve’s flow direction arrow points in the correct orientation.
Step 4: Secure the Valve with Flange Bolts
- Evenly tighten the flange bolts in a crisscross pattern to the recommended torque specifications.
- Ensure the valve is securely held in place and the connection is leak-tight.
Step 5: Perform a Leak Test
- Pressurize the system and check for any leaks around the flanged connections.
- Tighten the bolts further if necessary to eliminate any leaks.
Step 6: Complete the Installation
- Once the leak test is successful, the installation of the flanged check valve is complete.
- Ensure the valve is accessible for future maintenance and inspection.
The Operation Theory of Flanged Check Valve
The primary function of a flanged check valve is to allow fluid flow in one direction while preventing backflow. This is achieved through the valve’s internal mechanism, which is typically one of the following designs:
- Swing Check Valve: In a swing check valve, a hinged disc or flapper is held open by the forward flow of the fluid. When the flow reverses, the disc swings closed, creating a tight seal to prevent backflow.
- Ball Check Valve: Flanged check valves with a ball design feature a spherical ball that is held against the valve seat by the forward flow. When the flow reverses, the ball is pushed back, sealing the valve and stopping backflow.
- Lift Check Valve: Flanged check valves with a lift design use a guided piston or disc that is lifted off the valve seat by the forward flow. When the flow reverses, the piston or disc drops back down, sealing the valve.
- Flanged Dual Plate Check Valve: Flanged dual plate check valves have two hinged plates that open and close in response to the flow direction. The plates are held open by the forward flow and close when the flow reverses, preventing backflow.