Introduction to Trunnion Mounted Ball Valve
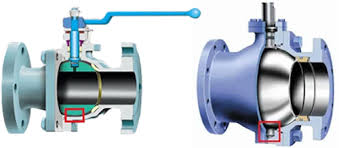
Introduction to Trunnion Mounted Ball Valve
A trunnion mounted ball valve is a type of industrial ball valve where the ball is supported on both ends by trunnions (bearing shafts). This design provides several advantages over a standard floating ball valve.
bonnet valve
symbol for check valve
The Application of Classification of Mounted Ball Valve
Mounted ball valves, such as the trunnion-mounted design, find widespread application across various industrial sectors. Their enhanced stability, higher pressure ratings, and reduced seat wear make them ideal for demanding environments. Industrial Ball Valves are commonly used in oil and gas, petrochemical, and power generation facilities, where reliable valve performance is crucial. For applications requiring exceptional pressure handling capabilities, High Pressure Ball Valves are the preferred choice. Meanwhile, High Temperature Ball Valves are specified for processes involving elevated temperatures, ensuring safe and efficient operation. Leading manufacturers like Cameron offer a comprehensive range of mounted ball valves, catering to the diverse needs of industrial customers and ensuring the smooth and safe flow of fluids and gases across a wide array of applications.
How to Select the Right Mounted Ball Valve?
When selecting the appropriate mounted ball valve for your application, several key factors must be considered. The required pressure rating, temperature range, and material compatibility are crucial. Additionally, the pipe size, flow requirements, and space constraints play a significant role in the selection process. Factors such as the level of shut-off required, the frequency of operation, and the overall system design should also be evaluated to ensure the chosen mounted ball valve meets the specific needs of the application. Consulting with valve experts or referring to industry standards can greatly assist in identifying the most suitable mounted ball valve for your particular requirements.
Features of Mounted Ball Valve
Stability:
The trunnion-mounted design provides enhanced stability, keeping the ball centered and reducing the risk of leakage even under high-pressure differentials across the valve.
Pressure Capabilities:
Mounted ball valves are engineered to withstand higher pressure and temperature conditions compared to their floating ball valve counterparts, making them suitable for more demanding applications.
Reduced Seat Wear:
The stabilized ball design in mounted ball valves leads to decreased seat wear, resulting in extended operational life and reduced maintenance requirements.
Larger Size Range:
Mounted ball valves are commonly available in larger sizes, up to 60 inches in diameter, making them a preferred choice for large-scale industrial processes.
Efficient Actuation:
The stabilized ball design of mounted ball valves requires less torque to operate, allowing for the use of smaller and more cost-effective actuators.
Versatility:
Mounted ball valves can handle a wide range of fluids, gases, and even steam, making them a versatile choice for various industrial applications.
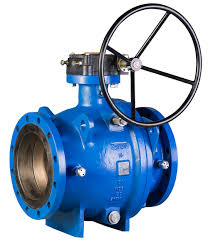
The Specifications of Mounted Ball Valve
Specification | Details |
---|---|
Type | Trunnion Mounted Ball Valve |
Ball Material | 316 Stainless Steel |
Attachment Type | Flanged |
Flange Standard | ANSI 150# |
Flange Size | 6 inch |
Body Material | Carbon Steel, ASTM A216 Grade WCB |
Safe for Use With | Liquids, Gases, Steam |
Handle Type | Gear Operated |
Handle Material | Carbon Steel |
Maximum Working Pressure | 720 psi |
Maximum Working Pressure | 50 bar |
Operating Pressure | 0-720 psi |
The Installation Steps for Mounted Ball Valve
Site Preparation:
Ensure the installation site is clean, free of debris, and the pipe ends are properly aligned and supported. Verify the valve orientation matches the intended flow direction.
Valve Inspection:
Carefully inspect the valve for any shipping damage or defects. Confirm the valve model, size, and materials are appropriate for the application.
Valve Positioning:
Position the valve between the flanges, ensuring proper alignment of the bolt holes. Insert the flange bolts and hand-tighten them in a crisscross pattern.
Bolt Tightening:
Using a torque wrench, tighten the flange bolts to the recommended torque values specified by the manufacturer, typically between 60-90 ft-lbs for a 6-inch ANSI 150# flange.
Valve Actuation:
Attach the actuator (manual, electric, or pneumatic) to the valve’s stem, ensuring a secure connection. Verify the actuator’s stroke and rotation direction match the valve’s open/close requirements.
Leak Testing:
Perform a low-pressure leak test on the valve installation to check for any potential leaks at the flange connections or stem packing. Gradually increase the pressure to the maximum working pressure and re-inspect.
Documentation:
Record the valve’s installation details, including the date, location, technician information, and any relevant comments for future reference and maintenance.
The Operation Theory of Mounted Ball Valve
Trunnion Design:
Mounted ball valves, such as the trunnion-mounted type, feature a ball that is supported on both ends by trunnions or journals. This design provides enhanced stability and control of the ball’s positioning within the valve body.
Pressure Balancing:
The trunnion design helps to balance the pressure across the ball, reducing the force required to operate the valve. This allows for the use of smaller and more cost-effective actuators.
Reduced Seat Wear:
The stabilized ball positioning minimizes the sliding contact between the ball and the seats, leading to decreased seat wear and extended operational life.
Heavy Duty Ball Valves:
Heavy-duty ball valves are designed to withstand the demands of industrial applications, such as those found in the oil and gas, petrochemical, and power generation industries. They feature robust construction, higher pressure and temperature ratings, and enhanced durability.
Pipeline Ball Valves:
Pipeline ball valves are specifically engineered for use in pipeline systems, where they provide reliable isolation and flow control. Their design considerations include compatibility with pipeline standards, ease of installation, and the ability to handle a wide range of pipeline media.