belly dump gate control valve
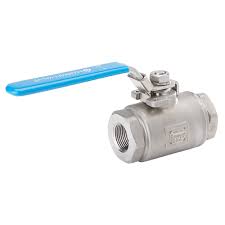
Standards
API 600 – Steel Gate, Globe, and Check Valves for Petroleum and Natural Gas Industries
ASME B16.10 – Face-to-Face and End-to-End Dimensions of Valves
ASME B16.5 – Pipe Flanges and Flanged Fittings
ASME B16.25 – Buttwelding Ends
API 598 – Valve Inspection and Testing
The Application of High Pressure Valve
Cameron, a renowned manufacturer of industrial valves, offers a comprehensive range of high pressure valves designed to handle demanding applications across various industries. These valves, featuring robust high pressure valve stems and advanced high pressure relief valve mechanisms, are engineered to withstand intense pressures and ensure reliable performance. Cameron’s high pressure valve solutions are widely utilized in oil and gas, petrochemical, and power generation sectors, where precise flow control and exceptional durability are critical. By leveraging cutting-edge technologies and materials, Cameron’s high pressure valves deliver unparalleled safety, efficiency, and longevity, making them the preferred choice for mission-critical applications that require the utmost in reliable valve performance.
What Are The Types Of High Pressure Valve?
Gate Valves: High pressure gate valves, such as the C5 model from Cameron, feature a forged steel construction and are designed to handle pressures up to 1,500 psi. They offer tight shutoff, corrosion resistance, and robust reliability.
Globe Valves: High pressure globe valves are suitable for throttling and flow control applications, providing precise regulation of fluid flow even at elevated pressures. They are often used in steam, gas, and liquid systems.
Ball Valves: High pressure ball valves are known for their quick, quarter-turn operation and tight sealing capabilities. They are commonly used for on/off control in high-pressure pipelines and process equipment.
Butterfly Valves: High pressure butterfly valves are compact, lightweight, and offer fast actuation for emergency shut-off and flow regulation in high-pressure systems.
Check Valves: High pressure check valves prevent backflow in high-pressure applications, ensuring unidirectional flow and protecting downstream equipment.
What Is High Pressure Valve?
A high pressure valve is a specialized type of industrial valve designed to withstand and control the flow of fluids, gases, or steam under extremely high pressure conditions, typically ranging from hundreds to thousands of pounds per square inch (psi). These valves are engineered with robust construction, How to Select the Right High Pressure Valve?sealing mechanisms, and specialized materials to ensure reliable operation and safety in applications where conventional valves may not be suitable. High pressure valves are widely used in industries such as oil and gas, petrochemical, power generation, and heavy manufacturing, where the ability to regulate and isolate high-pressure systems is critical for efficient and safe operation. By providing precise flow control and dependable shut-off capabilities, high pressure valves play a vital role in maintaining the integrity and performance of mission-critical industrial infrastructure.
How to Select the Right High Pressure Valve?
Selecting the right high pressure valve for an application requires careful consideration of several key factors. The operating pressure range, flow requirements, and the specific properties of the media being controlled are crucial in determining the appropriate valve type, size, and materials of construction. Additionally, factors such as valve actuation, end connections, and environmental Features of High Pressure Valvemust be taken into account to ensure the valve can withstand the demands of the high pressure system. Consulting with experienced valve manufacturers or distributors can provide valuable guidance in navigating the selection process, as they can offer expertise in matching the right high pressure valve solution to the unique requirements of the application. By carefully evaluating these considerations, end-users can ensure the selected high pressure valve delivers reliable, safe, and efficient performance for the intended use.
Features of High Pressure Valve
Robust Construction
High pressure valves feature reinforced bodies, bonnets, and internal components to withstand the immense forces and stresses associated with high-pressure applications.
Advanced Sealing Systems
Specialized seals, gaskets, and packing materials are employed in high pressure valves to maintain a tight, leak-free seal and prevent the escape of pressurized media.
Corrosion Resistance
The materials used in high pressure valves, such as stainless steel or specialized alloys, are chosen for their ability to resist corrosion and withstand the often harsh and aggressive fluids or gases encountered in high-pressure systems.
Precise Flow Control
High pressure valves are designed to provide accurate and reliable flow regulation, allowing for precise control of fluid or gas movement even under extreme pressure conditions.
Thermal Management
Some high pressure valve designs incorporate features to manage the heat generated by the high-pressure media, ensuring safe and efficient operation.
Reliable Actuation
High pressure valves can be equipped with a variety of actuation mechanisms, including manual, pneumatic, or hydraulic, to provide reliable and responsive control of the valve’s opening and closing.
Advantages and Disadvantages of High Pressure Valve
Advantages of High Pressure Valves:
Reliability: High pressure valves are engineered to withstand extreme pressure conditions, ensuring dependable and consistent performance in critical applications.
Precise Control: High pressure valves offer accurate flow regulation and shut-off capabilities, allowing for optimal control of high-pressure systems.
Durability: The robust construction and specialized materials used in high pressure valves contribute to their extended service life and resistance to wear and tear.
Safety: High pressure valves incorporate safety features and design considerations to mitigate the risks associated with high-pressure fluid or gas handling.
Versatility: High pressure valves can be adapted to a wide range of industries and applications, from oil and gas to power generation and beyond.
Disadvantages of High Pressure Valves:
Higher Cost: High pressure valves generally have a higher initial cost compared to their lower-pressure counterparts due to the specialized materials and manufacturing processes involved.
Maintenance Requirements: The complex design and specialized components of high pressure valves may require more frequent maintenance and inspection to ensure continued safe and reliable operation.
Limited Availability: Certain types or sizes of high pressure valves may have limited availability or longer lead times, which can impact project timelines and planning.
Increased Energy Consumption: The higher pressure requirements of some high pressure valve applications can result in increased energy consumption and operating costs.
The Specifications of High Pressure Valve
Specification | Details |
---|---|
Type | Ball Valve |
Ball Material | Stainless Steel (316) |
Attachment Type | Threaded |
Thread Standard | ASME B1.20.1 |
Thread Size | 1/2 inch NPT |
Body Material | Forged Carbon Steel |
Safe for Use With | Oil, Gas, Water, Steam |
Handle Type | Lever |
Handle Material | Steel with Vinyl Coating |
Maximum Working Pressure | 5,000 psi |
Maximum Working Pressure | 345 bar |
Operating Pressure | 3,000 – 4,500 psi |