Rising Stem Valves – Ball, Gate, vs. Non-Rising
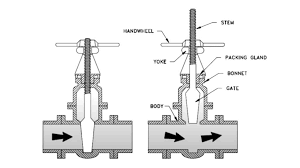
The Application of Rising Stem Valves
Introducing Rising Stem Valves, including non-rising stem gate valve and rising stem gate valve variations. These valves feature a stem mechanism that moves vertically as the valve opens or closes, providing a visual indication of the valve position. Cameron offers a wide range of rising stem valves designed for various applications, ensuring precise flow control and reliable performance. The rising stem valve design is particularly advantageous in situations where clear visibility of the valve position is essential, such as in critical industrial processes or emergency shutdown systems. With their robust construction and versatile functionality, Cameron rising stem valves are trusted for their durability and efficiency in diverse industrial environments.
What Are The Types Of Rising Stem Valves?
- Rising Stem Gate Valve: In this type, the stem rises vertically as the valve opens, providing a visual indication of the valve’s position. This design is commonly used in applications where precise flow control and visibility of the valve position are crucial.
- Non-Rising Stem Gate Valve: Unlike the rising stem gate valve, the stem of this valve remains stationary while the gate moves up and down to control the flow of fluid. This type of valve is often preferred in underground or confined spaces where vertical stem movement is restricted.
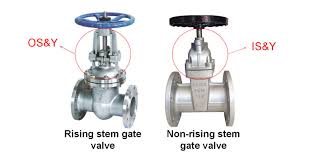
What Is Rising Stem Valves?
Rising stem valves are a type of industrial valve distinguished by their stem mechanism, which moves vertically as the valve opens or closes. This movement provides a visible indication of the valve’s position, aiding in monitoring and control. Rising stem valves are widely utilized in numerous industries for their precise flow control and operational reliability.
How Does Rising Stem Valves?
Rising stem valves operate by utilizing a stem mechanism that moves vertically as the valve opens or closes. As the handwheel or actuator is turned, the stem rises or descends, lifting or lowering the valve closure mechanism to control the flow of fluid. This vertical movement provides a visual indication of the valve’s position, facilitating monitoring and operation. Rising stem valves are widely employed in industrial settings for their precise flow control and ease of operation.
Features of Rising Stem Valves
- Visibility: The vertical movement of the rising stem provides a clear visual indication of the valve’s position, aiding in monitoring and control.
- Durability: Constructed with robust materials, these valves offer excellent resistance to wear, corrosion, and harsh operating conditions.
- Reliability: The straightforward design of rising stem valves ensures dependable performance and minimal maintenance requirements.
- Ease of Operation: The vertical stem movement makes it easy to operate the valve manually or through automated systems, enhancing overall efficiency.
- Versatility: Available in various sizes, materials, and configurations, rising stem valves are suitable for a wide range of applications across different industries.
- Sealing: The stem and packing gland arrangement provides effective sealing, minimizing the risk of leaks and ensuring fluid containment.
- Compatibility: These valves are compatible with different fluids and operating temperatures, making them adaptable to diverse operational environments.
Advantages and Disadvantages of Rising Stem Valves
Advantages:
- Visible Position: The vertical stem movement offers a clear indication of the valve’s position, aiding in monitoring and control.
- Reliable Operation: Rising stem valves are known for their dependable performance and minimal maintenance requirements.
- Ease of Operation: The straightforward design makes these valves easy to operate manually or through automated systems.
- Durability: Constructed with robust materials, rising stem valves offer excellent resistance to wear, corrosion, and harsh operating conditions.
- Versatility: Available in various sizes, materials, and configurations, they are suitable for a wide range of applications across different industries.
Disadvantages:
- Space Requirements: The vertical movement of the stem may require additional space above the valve, limiting installation options in confined areas.
- Potential for Damage: External factors such as debris or improper handling may cause damage to the stem mechanism, affecting valve operation.
- Maintenance: While generally low maintenance, rising stem valves may require periodic inspection and lubrication to ensure proper functioning.
- Complexity in Design: Some variants of rising stem valves with intricate designs may be more challenging to maintain or repair.
The Specifications of Rising Stem Valves
Specification | Details |
---|---|
Type | Rising Stem Valve |
Ball Material | N/A |
Attachment Type | Flanged, Threaded, Welded, Grooved |
Thread Standard | N/A |
Thread Size | N/A |
Body Material | Carbon Steel, Stainless Steel, Brass, Bronze, PVC, etc. |
Safe for Use With | Water, Oil, Gas, Chemicals, Steam, etc. |
Handle Type | Handwheel, Gear Operator, Actuator |
Handle Material | Carbon Steel, Stainless Steel, Aluminum, Plastic, etc. |
Maximum Working Pressure (psi) | Specific to valve size and design |
Maximum Working Pressure (bar) | Specific to valve size and design |
Operating Pressure | Varies based on application requirements |
The Installation Steps for Rising Stem Valves
- Preparation: Gather all necessary tools and equipment, including wrenches, bolts, nuts, and gaskets required for the installation.
- Location Selection: Choose a suitable location for installing the valve, ensuring adequate space for operation and maintenance.
- Valve Inspection: Thoroughly inspect the rising stem valve, checking for any damage, defects, or debris that could affect its performance.
- Seal Inspection: Verify the condition of the sealing components, such as gaskets or packing glands, ensuring they are clean and in good condition.
- Alignment: Ensure proper alignment of the valve with the piping system, using alignment marks or indicators if necessary.
- Attachment: Securely attach the valve to the piping system using appropriate fasteners, such as bolts or screws, following the manufacturer’s specifications.
- Tightening: Gradually tighten the fasteners in a crisscross pattern to evenly distribute the load and ensure a secure fit without damaging the valve or the piping.
- Connection: Connect the valve to the actuator or control system, ensuring proper alignment and functionality.
- Testing: Perform a pressure test to verify the valve’s performance under operating conditions, ensuring it can withstand the maximum working pressure without leaking or failing.
- Documentation: Record the installation details, including torque values, pressure test results, and any other relevant information for future reference and maintenance.
The Operation Theory of Rising Stem Valves
- Gate Valve with Non-Rising Stem: In this type of valve, the stem remains stationary while the gate moves up and down to control the flow of fluid. When the handwheel or actuator is turned, it activates the threaded stem, causing the gate to either rise or descend to open or close the valve.
- Gate Valve with Rising Stem: In contrast, gate valves with a rising stem have a stem mechanism that moves vertically as the valve opens or closes. As the handwheel or actuator is turned, the stem rises or descends, lifting or lowering the gate to regulate the flow of fluid. This vertical movement provides a visual indication of the valve’s position, aiding in monitoring and control.
The Parameters Chart of Rising Stem Valves
Parameter | Material Options |
---|---|
Valve Type | Rising Stem Valve |
Stem Material | Stainless Steel, Carbon Steel, Alloy Steel, Brass, Bronze, etc. |
Body Material | Stainless Steel, Carbon Steel, Alloy Steel, Brass, Bronze, PVC, etc. |
Seat Material | PTFE, Graphite, Metal, Soft Seated, Fire-Safe, etc. |
Packing Material | PTFE, Graphite, Carbon, Aramid, GFO, etc. |
Bolting Material | Stainless Steel, Carbon Steel, Alloy Steel, Brass, etc. |
Gasket Material | Non-Asbestos, Spiral Wound, Graphite, PTFE, etc. |