Electric High Pressure Control Valve
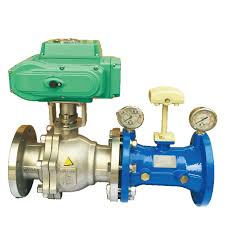
The Application of Electric High Pressure Control Valve
Introducing Cameron’s Electric High Pressure Control Valve, engineered to manage demanding applications requiring precise flow regulation under extreme pressures. Our high pressure control valves offer unparalleled reliability and accuracy, ensuring optimal performance in critical industrial processes. Whether it’s controlling fluid flow in hydraulic systems, oil and gas pipelines, or chemical processing plants, trust Cameron for innovative solutions tailored to your high-pressure needs.
What Are The Types Of Electric High Pressure Control Valve?
- Electric Globe Control Valve: Offers precise flow control in high-pressure systems, commonly used in industries such as oil and gas, power generation, and chemical processing.
- Electric Ball Control Valve: Features a spherical closure mechanism for efficient flow regulation in high-pressure applications, suitable for use in pipelines and industrial processes.
- Electric Butterfly Control Valve: Utilizes a disc-shaped closure mechanism to control flow in high-pressure systems, providing reliable performance in various industries, including water treatment, HVAC, and manufacturing.
- Electric Diaphragm Control Valve: Employs a flexible diaphragm to regulate flow in high-pressure environments, ideal for applications requiring tight shut-off and precise control.
- Electric Pinch Control Valve: Utilizes a pinching mechanism to control flow by compressing a flexible tube, suitable for handling abrasive or corrosive fluids in high-pressure conditions.
What Is Electric High Pressure Control Valve?
An Electric High Pressure Control Valve is a specialized valve designed to regulate the flow of fluid in systems operating under high pressure conditions. Equipped with an electric actuator, it offers precise control and adjustment of flow rates, ensuring optimal performance and safety in industrial processes such as oil and gas, chemical processing, and power generation.
How to Select the Right Electric High Pressure Control Valve?
Selecting the right Electric High Pressure Control Valve involves considering factors such as the maximum pressure rating, flow capacity, material compatibility, and actuation type. Evaluate the specific requirements of your application, including pressure range, fluid type, and operating conditions, to ensure the chosen valve meets performance and safety standards. Additionally, consult with experts to assess the compatibility with existing systems and integration capabilities.
Features of Electric High Pressure Control Valve
- High Pressure Capability: Designed to withstand and regulate fluid flow in high-pressure environments, ensuring reliable performance under demanding conditions.
- Precision Control: Offers precise and accurate flow control, allowing for fine adjustments to meet specific process requirements and maintain system stability.
- Electric Actuation: Equipped with an electric actuator, enabling remote operation and integration with control systems for automated flow regulation.
- Diverse Applications: Suitable for a wide range of industries and applications, including oil and gas, chemical processing, power generation, and more, due to its versatility and adaptability.
- Robust Construction: Constructed from high-quality materials such as stainless steel or alloy, ensuring durability and longevity even in harsh operating conditions.
- Safety Features: Incorporates safety features such as fail-safe mechanisms or emergency shut-off options to prevent system failures or accidents in critical situations.
- Easy Maintenance: Designed for easy maintenance and servicing, with accessible components and straightforward repair procedures to minimize downtime and ensure continuous operation.
Advantages and Disadvantages of Electric High Pressure Control Valve
Advantages:
- Precise Control: Electric high pressure control valves offer precise regulation of fluid flow, ensuring optimal process performance and efficiency.
- Remote Operation: Equipped with electric actuators, these valves enable remote operation and integration with control systems, allowing for automation and remote monitoring.
- Versatility: Suitable for a wide range of applications and industries, providing flexibility and adaptability to diverse operating conditions.
- Safety: Incorporate safety features such as fail-safe mechanisms or emergency shut-off options to enhance system safety and prevent accidents.
Disadvantages:
- Cost: Electric high pressure control valves can be more expensive upfront compared to other types of valves, especially for larger sizes or specialized designs.
- Power Dependency: Reliance on electrical power for operation may pose a risk in the event of power outages, requiring backup systems or redundancy to ensure continuous operation.
- Complexity: The integration of electric actuators and control systems adds complexity to the valve assembly, potentially increasing maintenance and troubleshooting requirements.
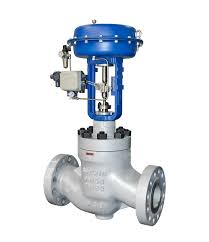
The Specifications of Electric High Pressure Control Valve
Specification | Details |
---|---|
Type | Globe, Ball, Butterfly, Diaphragm, etc. |
Ball Material | Stainless Steel, Alloy, Ceramic, etc. |
Attachment Type | Flanged, Threaded, Welded, etc. |
Thread Standard | ANSI, DIN, JIS, BS, etc. |
Thread Size | Specific measurement (e.g., 1 inch, 25 mm) |
Body Material | Carbon Steel, Stainless Steel, Alloy, etc. |
Safe for Use With | Compatible fluids, gases, or chemicals |
Handle Type | Lever, Handwheel, Electric Actuator, etc. |
Handle Material | Stainless Steel, Aluminum, Plastic, etc. |
Maximum Working Pressure (psi) | Specific value (e.g., 3000 psi) |
Maximum Working Pressure (bar) | Specific value (e.g., 207 bar) |
Operating Pressure | Range of pressure at which the valve operates effectively |
The Installation Steps for Electric High Pressure Control Valve
- Preparation: Ensure the work area is clean and free of debris. Gather all necessary tools and equipment for installation.
- Valve Inspection: Thoroughly inspect the Electric High Pressure Control Valve for any signs of damage or defects before installation.
- Valve Positioning: Determine the optimal location for installing the valve within the piping system, considering factors such as accessibility and flow direction.
- Pipe Preparation: Prepare the pipe ends by cleaning and deburring them to ensure a proper seal with the valve connections.
- Connection: Attach the valve to the pipeline using the appropriate attachment type (flanged, threaded, welded, etc.), ensuring a secure and leak-free connection.
- Sealing: Apply sealing materials such as gaskets or thread sealant to the valve connections to prevent leaks.
- Alignment: Align the valve body with the pipeline to ensure proper flow alignment and minimize stress on the valve components.
- Tightening: Use calibrated torque wrenches to tighten the valve connections to the manufacturer’s recommended torque specifications, ensuring a secure fit without over-tightening.
- Electrical Connection: If applicable, connect the electric actuator to the power source according to the manufacturer’s instructions, ensuring proper grounding and electrical safety.
- Testing: Conduct a pressure test and functional test to verify the integrity and performance of the installed Electric High Pressure Control Valve before putting it into service.
The Operation Theory of Electric High Pressure Control Valve
- Electric High Pressure Control Valve Operation Theory:
- The valve operates by using an electric actuator to adjust the position of the valve mechanism, controlling the flow of fluid through the system.
- When an electrical signal is sent to the actuator, it translates into mechanical motion, causing the valve to open or close to a specific degree.
- This precise control over the valve’s position allows for accurate regulation of flow rates, maintaining desired pressure levels within the system.
- DD15 High-Pressure Fuel Pump Quantity Control Valve:
- Specifically designed for diesel engines like the DD15, this valve controls the quantity of fuel delivered to the engine’s high-pressure fuel pump.
- It operates in conjunction with the engine control unit (ECU), which sends signals to adjust the valve’s position based on engine operating parameters such as speed, load, and temperature.
- By regulating the amount of fuel supplied to the high-pressure pump, the valve helps optimize engine performance, fuel efficiency, and emissions.
- Common Features:
- Both the Electric High Pressure Control Valve and the DD15 High-Pressure Fuel Pump Quantity Control Valve utilize precise actuation mechanisms to adjust flow rates accurately.
- They are designed to withstand high-pressure conditions and provide reliable performance in demanding industrial applications or engine systems.